Researchers utilize perovskites to drastically reduce carbon dioxide (CO2) emissions from existing iron and also steel furnaces
- Researchers from the UK's University of Birmingham, in collaboration with China's University of Science & Technology Beijing, have utilized perovskite materials to develop a novel adjustment for existing iron and steel furnaces that could reduce carbon dioxide (CO2) emissions from the steelmaking industry by almost 90%.
This radical reduction is attained with a 'shut loop' carbon recycling system, which can change 90% of the coke normally utilized in current blast furnace-basic oxygen furnace systems and produces oxygen as a biproduct.
Devised by Professor Yulong Ding and Dr. Harriet Kildahl from the University of Birmingham's School of Chemical Engineering, the system can supply significant cost savings while reducing total emissions.
Professor Ding claimed: "Current proposals for decarbonizing the steel field rely on terminating existing plants and also presenting electrical arc furnaces powered by renewable electricity. Nonetheless, an electric arc furnace plant can set you back over ₤ 1 billion to construct, which makes this switch economically unfeasible while staying to meet the Paris Climate Agreement. The system we are recommending can be retrofitted to existing plants, which reduces the risk of stranded assets, as well as both the decrease in CO2, and also the cost financial savings, are seen quickly."
The novel recycling system captures the CO2 from the top gas as well as reduces it to CO utilizing a perovskite material. A double perovskite, Ba2Ca0.66 Nb0.34 FeO6, was proposed for the thermochemical splitting of CO2, a viable candidate because of its reduced reaction temperatures, high carbon monoxide (CO) returns, as well as 100% selectivity towards CO
A lot of the world's steel is produced utilizing blast furnaces which produce iron from iron ore and also basic oxygen furnaces which transform that iron into steel. The process is naturally carbon extensive, using metallurgical coke produced by destructive distillation of coal in a coke stove, which reacts with the oxygen in the hot air blast to produce carbon monoxide. This responds with the iron ore in the furnace to produce CO2. The top gas from the furnace consists of mostly nitrogen, CO as well as CO2, which is burned to elevate the air blast temperature level approximately 1200 to 1350oC in a hot stove before blown to the furnace, with the CO2 and N2 (likewise having NOx) gave off to the environment.
Under a high concentration of CO2, the perovskite splits CO2 right into oxygen, which is absorbed into the lattice, as well as CO, which is fed back into the blast furnace. The perovskite can be regrowed to its original form in a chain reaction that happens in a reduced oxygen setting. The oxygen produced can be made use of in the basic oxygen furnace to produce steel.
The new system can be retrofitted to existing furnaces, with the enhancement of an array of extra gas separators and also heat exchangers required to support the perovskite splitter.
University of Birmingham Enterprise has actually submitted a patent application covering the system and its use in metal production and also is seeking lasting partners to participate in pilot studies, provide this technology to existing infrastructure, or work together on further research to develop the system.
Also read
- FTC Solar Launches Hurricane-Resistant Solar Tracker System
- Study flags “no-clean” flux as TOPCon corrosion risk under damp heat
- Lead-Free Solar Cells Achieve Breakthrough 33% Efficiency
- Leapting Robots Revolutionize Middle East Solar Installation
- Cosmic Veil Coating Boosts Perovskite Solar Cells for Space Missions
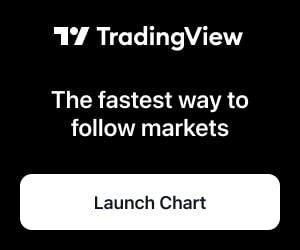