New Laser-Based Contacting Process Developed for Solar Cells
- The Fraunhofer Institute for Solar Energy Systems ISE has actually created an alternate process for creating solar battery calls. The laser transfer as well as shooting (LTF) method offers numerous benefits contrasted to conventional procedures, specifically for specific solar cell surface areas. Along with market partners in the joint project "C3PO", the Fraunhofer scientists in Freiburg have realized a totally automated LTF procedure for the first time on a system from Pulsar Photonics GmbH. Currently the process can be systematically examined and also maximized with the goal of industrial execution. f-cell conference in Stuttgart on September 29.
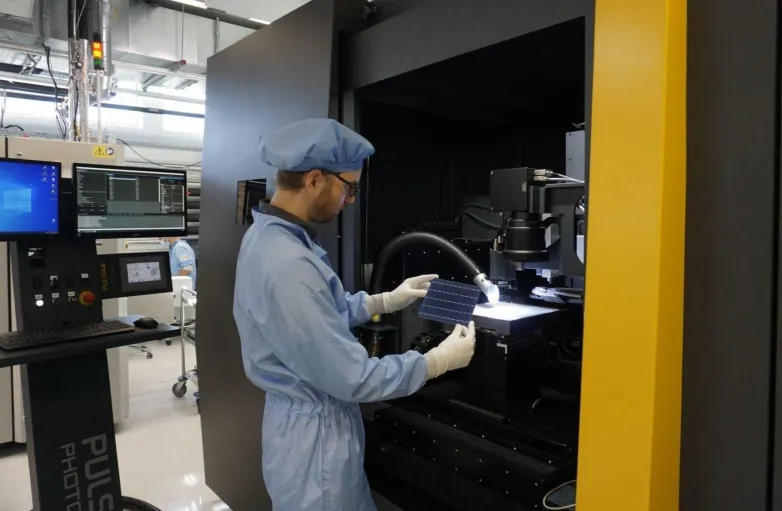
Get in touch with fingers, conductive lines made of steel, are put on the solar battery surface area to carry the produced solar battery existing out of the cell. The standard process for creating the get in touch with fingers is screen printing, in which silver paste is used via a filter onto the front side of the solar cell. Given that solar cell production is just one of the biggest consumers of silver worldwide, there is terrific interest to discover alternative metals as well as various other treatments for using metal calls. Among these is a process called electrochemical plating. As a rule, solar batteries are framed in an electrically insulating finishing that needs to be opened to make the contact fingers. For conventional plating procedures, a laser is usually made use of to open the coating. The get in touch with fingers are electrochemically grown at these openings making use of first nickel, after that copper and lastly silver.
Making use of the laser transfer and shooting (LTF) process to open the shielding layer and develop the steel contact fingers has several advantages over the standard technique. For one, it enables better versatility in the selection of get in touch with steels: allowing light weight aluminum, titanium, or bismuth to be used rather than nickel, for instance. Compared to screen printing, the LTF process enables much more versatility in the design of the call fingers. The metallization process is likewise suitable for solar batteries with temperature-sensitive layers, as it does not heat the solar cell above space temperature level.
The LTF Process
The LTF process includes 2 steps: In the very first step, a straight laser printing process is utilized to transfer steel in the wanted get in touch with finger layout from a metal-coated aluminum foil to a solar battery. At this point, the process is originally referred to as LIFT (Laser Induced Forward Transfer). It is necessary that the transferred steel structures are really narrow to make sure that the cell area is not excessively shady. „ In the research laboratory, we were able to use steel lines of less than 5 µm size to the solar battery," reports Dr. Saskia Kühnhold-Pospischil, task supervisor at Fraunhofer ISE. For the LIFT process in the new system, the solar battery is positioned on a vacuum cleaner chuck and also is relocated under a metal-coated foil where the metal is transferred to the solar battery. After the steel transfer, the steel aluminum foil is delivered totally immediately via a roll-to-roll system for the steel transfer of the following solar battery. The covered films used in the LIFT process were created particularly for this objective by the ROWO firm.
In the second process action, the steel frameworks from the initial step are formed into calls using a laser selective heating (LSH) procedure. A laser from the Soliton/ Advalue company is utilized. The wavelength of the laser beam of light is absorbed by the metal but not by the underlying silicon. Consequently, the laser does not harm the silicon product in this procedure, which is useful for high solar cell effectiveness. Both procedure steps can be completely automated as well as are carried out in the brand-new LTF system aligned to within a few micrometers.
The capability of the LTF procedure had actually been proven formerly in the laboratory. Currently it has been carried out for the very first time on an industry-scale system as a joint effort between the job partners PULSAR, Soliton, RENA, ROWO and Fraunhofer ISE within the joint task „ C3PO" ("Cool Copper Contacts-- Development of a commercial low-temperature innovation to manufacture 20µm copper get in touches with for bifacial PERC, hetero and TOPCon solar batteries"), which was moneyed by the Federal Ministry for Economic Affairs and Energy BMWi. In future, along with the LTF application defined over, contact fingers are also to be produced in their totality layer by layer, thus additively." In addition to the manufacture of tiny 3D frameworks as well as the localized finish of sensitive components, we see feasible applications for the LTF innovation in a selection of other research fields. With the pilot system and our consortium of specialists, we hold the most effective prerequisites to successfully create these in the future," states Jan Nekarda, department head of Structuring as well as Metallization at Fraunhofer ISE.
Also read
- Fraunhofer ISE Unveils LED Method To Calibrate Tandem Solar Modules
- Researchers unveil tougher perovskite glass brick for solar façades applications
- FTC Solar Launches Hurricane-Resistant Solar Tracker System
- Study flags “no-clean” flux as TOPCon corrosion risk under damp heat
- Lead-Free Solar Cells Achieve Breakthrough 33% Efficiency
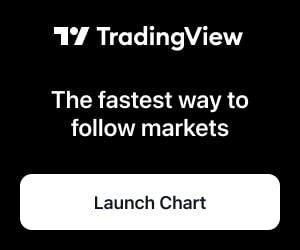