Monolithic perovskite-silicon solar cell with 20% effectiveness via new lamination method
- The solar cell accomplished an open-circuit voltage of 1.75 V, a short-circuit present density of 15.5 mA cm − 2, and a fill element of 73.6%. It was likewise able to retain 93% of its first performance after 100 hrs at a temperature of 80 C.
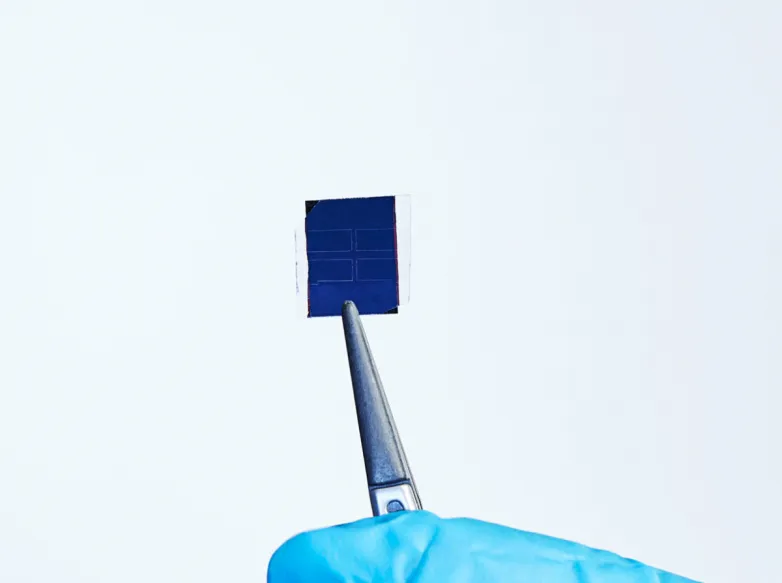
A group of scientists from the Karlsruhe Institute of Technology (KIT) and the Forschungszentrum Jülich GmbH in Germany has actually developed a monolithic perovskite-silicon solar cell with a power conversion performance of 20% via a new lamination method.
" In our work, we examine exactly how this lamination process can be related to the highly appealing perovskite/silicon tandem technology," the research study's corresponding author, Uli Paetzold, informed pv magazine. "The presented solar cells are the extremely first prototypes as well as highlight that lamination is an appropriate alternative construction method for monolithic perovskite/silicon tandem solar cells. The lamination approach is specifically intriguing for perovskite-based PV, as it notably raises the degree of freedom in the option of materials and easily accessible deposition techniques."
With the recommended method, the cell's useful layers such as charge transportation products, electrodes, as well as perovskite absorbers are refined in the same way as in devices produced making use of the basic consecutive layer deposition technique. "The laminated tandem device includes 2 separately generated half-stacks hot-pressed together," the researchers claimed. "The mix of warm and also pressure advertises perovskite recrystallization, thus producing an intimate call at the interface."
They applied pressure of 80 MPa and a temperature of 90 C throughout lamination for a duration of 5 mins as well as asserted this procedure is beneficial to the perovskite morphology, as it reduces non-radiative recombination losses. "The perovskite thin-film recrystallizes as well as joins both half-stacks into a monolithic perovskite/silicon tandem solar cell," they described, keeping in mind that the origin imply square (RMS) roughness of perovskite film decreased from 20.0 to 1.7 nm after lamination, which the grain size of perovskite increased from 284 to 350 nm.
The laminated cell achieved an effectiveness of 20.0%, an open-circuit voltage of 1.75 V, a short-circuit existing density of 15.5 mA centimeters − 2, and also a fill factor of 73.6%. "As anticipated in a monolithic tandem device, the open-circuit voltage of the tandem solar cell nears the sum of the voltage of both sub-cells," the researchers defined. Additionally, the device was able to preserve 93% of its first effectiveness after 100 hrs at a temperature of 80 C.
The researchers additionally kept in mind that the solar cell likewise exhibited negligible hysteresis-- a result that afflicts perovskite devices since their outcome depends upon a variety of previous inputs instead of just their instant problem, rendering efficiency less predictable. In perovskite cells, hysteresis is purely depending on the composition of the product. Ion migration and also non-radiative recombination near user interfaces are typically thought about responsible for the effect.
They introduced the lamination procedure in the paper "Laminated Monolithic Perovskite/Silicon Tandem Photovoltaics," published in Advanced Energy Materials. "Our work leads the way for new tandem device architectures to more improve power conversion efficiencies as well as device security," Paetzold claimed. "To date, laminated perovskite solar cells are made at lab-scale and also up-scaling is one of the following steps in additional advancement of this technique. In fact, lamination using hot-pressing is a very easy manufacture route, which allows manufacturing in parallel of the device half-stacks and also supplies a feasible straight encapsulation. If we compare it to developed industrial technologies like lamination for encapsulation or roll-to-roll procedures, the lamination approach seems to be fully appropriate for future commercial manufacturing."
Also read
- Fraunhofer ISE Unveils LED Method To Calibrate Tandem Solar Modules
- Researchers unveil tougher perovskite glass brick for solar façades applications
- FTC Solar Launches Hurricane-Resistant Solar Tracker System
- Study flags “no-clean” flux as TOPCon corrosion risk under damp heat
- Lead-Free Solar Cells Achieve Breakthrough 33% Efficiency
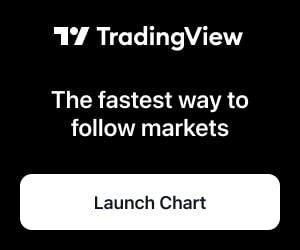