In the direction of more effective, non-toxic, and flexible thin-film solar cells
- Climate change, among the major global worries today, has actually made it clear that fossil fuels are harmful to our atmosphere and are not a sustainable source of power. It is important to adopt clean sources of power, and also solar cells are a prominent prospect on this front.
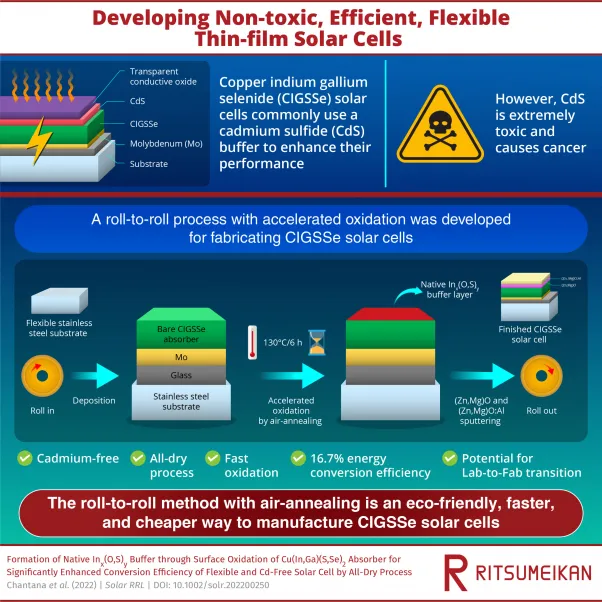
While performance is a main issue for solar cells, scientists have actually also concentrated on creating solar cells that are lightweight, inexpensive, and flexible. Nevertheless, the construction process itself has presented a major ecological worry: specifically, making use of toxic materials and also generation of industrial waste.
For example, copper indium gallium selenide (CIGSe) is a thin-film solar cell that supplies numerous benefits over standard silicon solar cells. Thin-film solar cells are about 100 times thinner, more affordable to make, and are much easier to mount on roofs and also vehicles. Additionally, contrasted to other solar materials made use of in thin-film solar cells like amorphous silicon, cadmium-telluride, and also organic materials, CIGSe absorbs light more highly and also can be prepared into thinner films. Nonetheless, they consist of a buffer layer of cadmium sulfide, which is extremely poisonous and cancer causing. This makes searching for choice, non-toxic materials important for large production and installment of CIGSe panels.
For Professors Jakapan Chantana and Takashi Minemoto at Ritsumeikan University, Japan, getting rid of cadmium from solar cells was as vital as establishing an eco-friendly production process that is both effective and also economical. Addressing these issues in a brand-new research study, a research study team led by them established a strategy in which the typical cadmium sulfide barrier layer was replaced with an indigenous barrier layer created by oxidizing the surface of the Cu(In, Ga)(S, Se)2 CIGSSe layer with an air-annealing procedure. The research was released on March 26, 2022, in the journal Solar RRL.
While attempts to oxidize the CIGSSe layer have actually been made before, the surface usually takes months to oxidize. With the new approach, nonetheless, the group minimized the oxidation time to a couple of hours, allowing for a much faster manufacturing by a "roll-to-roll" process. In this procedure, a CIGSSe layer is at first transferred on a flexible stainless-steel substrate. The deposition is after that followed by an air-annealing process where the surface area of the CIGSSe layer is oxidized to form native buffer layers of Inx(O, S)y. By try out different oxidation problems, the researchers fabricated a CIGSSe solar cell with a maximum energy conversion effectiveness of 16.7% after 6 hours of oxidation at 130 ° C.
"We have disclosed for the very first time that the CIGSSe surface oxidized via an optimized air-annealing procedure leads to a strong improvement in energy conversion performance," says Prof. Minemoto.
Although the reported performance is less than that of conventional solar cells (which commonly surpass 20%), the industrialized technique takes care of to do away with cadmium, making the solar cells eco-friendly. "In the standard process, cadmium is transferred on the CIGSSe layer via a chemical bathroom deposition procedure. By eliminating this step, we have actually developed a totally dry production process that produces much less waste," discusses Prof. Chantana. Additionally, the process is also cost-effective.
In order to make solar energy a feasible resource of clean energy, photovoltaic panels should come to be a lot more effective, affordable, and eco-friendly. "The method established in our research study can be scaled to large-scale production applications, which is what we require to make solar cells a clean power source not only in Japan but around the globe," concludes Prof. Minemoto.
Also read
- UbiQD Secures Landmark Quantum Dot Deal with First Solar
- Astronergy Invests $53M in Tandem Solar Cell Project
- ARENA Unveils $39M Solar Innovation Funding Round
- CNNP Optoelectronics brings utility-scale perovskite modules out of the lab
- Low-Temperature Sequential Deposition Lifts Inverted Perovskite Solar Cells Efficiency Record
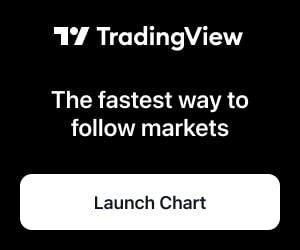