Environment-friendly solvent for a 16.7% perovskite solar cell
- Researchers in Germany aimed to get rid of making use of harmful solvents in the manufacturing of perovskite solar cells, changing them with a much more environmentally worldly called dimethyl sulfoxide (DMSO) which has so far shown difficult to integrate right into processes appropriate for large-scale production.
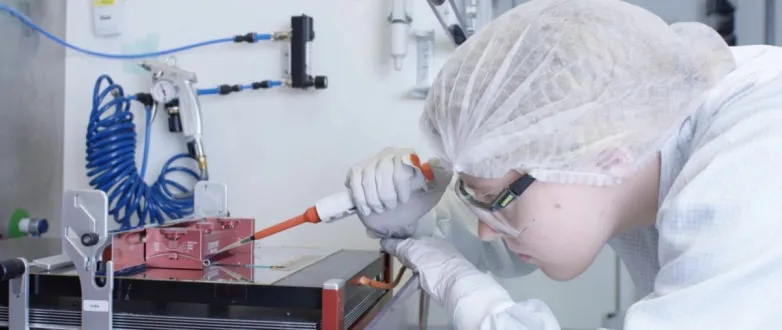
The group demonstrated a scalable blade layer process using DMSO as the only solvent, and also got to cell efficiencies close to those achieved making use of extra harmful materials.
Since their manufacture needs significantly much less energy than crystalline silicon solar products, perovskite solar cells are already seen by several as part of a much greener future for the solar industry. Nevertheless, The use of poisonous products in solvents is one resource of environmental concerns as perovskites relocate better to industrial production.
The precursor materials for the perovskite solar cell need to be dissolved in a solvent to be uniformly applied to a substrate. These solvents frequently include dimethylformamide (DMF), which is toxic to people as well as the environment. In production, its risk-free treatment and disposal would cause boosted prices for the solar cells in the long run.
Researchers led by Germany's Center for Solar Energy and Hydrogen Research Baden Württemberg (ZSW) looked for a product with unusual of buildings of being both non-toxic and also ideal as an industrial solvent, deciding on dimethyl sulfoxide (DMSO), which has currently been used in conjunction with other solvents in perovskite cell manufacturing, yet is more tough to make use of by itself.
" DMSO really looks to be unsuitable for this finish procedure. It is a solvent with high surface area stress and viscosity, which leaves an unequal layer transferred on the solar cell," the group explained. "DMSO also makes it hard to regulate the condensation procedure, which often causes little perovskite crystals and also a cell that produces much less solar energy."
Blade covering
The team's trying outs DMSO are described in the paper One-Step Blade Covering of Inverted Double-Cation Perovskite Solar Cells from a Green Precursor Solvent, released in Applied Energy Materials.
By customizing the movie development as well as drying out procedures they were able to conquer these problems, "We used a surfactant constructed from silicon oxide nanoparticles to layer the perovskite solar cell as well as adapted the drying out procedure," said ZSW scientist Jan-Philipp Becker. "With these 2 renovations, the procedure now generates consistent layers with big crystallites."
Using a blade coating process to use the liquified cell material to a glass substrate, the group achieved 16.7% efficiency, a solid result compared to the 16.9% it accomplished making use of DMF as a solvent. The cells produced in this research study gauged 0.24 cm ².
The group's next challenge will be to show larger devices generated via the same process, and it is now targeting mini modules determining 30 centimeters x 30 cm. "These new research findings are an essential turning point on the path to commercial production," said Becker. "Currently we will even more optimize the production procedure as well as produce larger modules."
Also read
- FTC Solar Launches Hurricane-Resistant Solar Tracker System
- Study flags “no-clean” flux as TOPCon corrosion risk under damp heat
- Lead-Free Solar Cells Achieve Breakthrough 33% Efficiency
- Leapting Robots Revolutionize Middle East Solar Installation
- Cosmic Veil Coating Boosts Perovskite Solar Cells for Space Missions
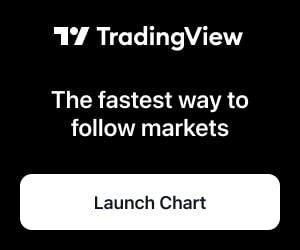