Breakthrough Cooling Technique Enhances Perovskite Wafer Quality
- Discover a groundbreaking method for crafting high-purity perovskite wafers with exceptional X-ray detection sensitivity, paving the way for innovative electronic and optoelectronic applications.
Researchers at Dongguan University of Technology and Xi'an Jiaotong University in China have introduced a novel spontaneous cooling method paired with hot-pressing to create high-purity, pinhole-free perovskite wafers. This innovative technique allows customization of wafers in sizes of 10, 15, and 20 mm by altering the mold and can be applied to various types of perovskites, including organic-inorganic and lead-free variants.
The team demonstrated that the lead-free Cs3Cu2I5 wafers exhibited impressive X-ray detection capabilities, achieving a high sensitivity of 3433.6 µC Gyair-1 cm-2 and a minimal detection limit of 33.17 nGyair s-1. Additionally, these wafers displayed excellent environmental resilience and stability, even without encapsulation, positioning them for potential integration into electronic and optoelectronic devices, thereby advancing the practical use of perovskite X-ray detectors.
How does the new cooling method enhance perovskite wafer production and performance?
Enhancements from the New Cooling Method in Perovskite Wafer Production and Performance
- Improved Crystal Quality: The spontaneous cooling method allows for a more uniform temperature gradient during the cooling phase, resulting in higher crystal quality and fewer defects in the perovskite structure. This ultimately leads to better electronic properties.
- High Purity: By minimizing the temperature fluctuations that can introduce impurities during the crystallization process, this method enhances the purity of the perovskite materials. High-purity wafers are crucial for optimizing the performance of electronic components.
- Scalability: The new cooling approach is adaptable for larger batch sizes without compromising quality, making it viable for industrial-scale production. This scalability is essential for meeting the growing demand for perovskite-based devices in the renewable energy sector.
- Custom Sizing Flexibility: The ability to easily alter the mold to produce wafers of different sizes (10, 15, and 20 mm) provides flexibility for specific applications. Manufacturers can tailor the wafers to fit the requirements of various electronic and optoelectronic devices, enhancing usability.
- Versatility with Different Chemistries: The method can be applied to various compositions of perovskites, including organic-inorganic and lead-free variants. This versatility opens up avenues for developing safer and more sustainable materials that meet environmental regulations.
- Enhanced Device Performance: The resulting pinhole-free structure of the wafers enhances charge transport efficiency, which is essential for applications in detectors and solar cells. This structural integrity supports higher efficiency rates in converting energy or detecting signals.
- Environmental Stability: The perovskite wafers produced using this cooling method have shown remarkable resilience to environmental challenges such as humidity and temperature fluctuations. This stability reduces the need for protective encapsulation, lowering production costs while maintaining performance.
- Promising Applications in X-ray Detection: The lead-free Cs3Cu2I5 wafers produced through this method have demonstrated exceptional detection capabilities, suggesting their potential to revolutionize X-ray imaging technologies in medical and security fields.
- Integration Potential: With their high sensitivity and minimal detection limits, these wafers are well-suited for integration into electronic and optoelectronic devices, paving the way for advanced applications in sensing technologies and renewable energy systems.
- Facilitation of Research and Development: The innovation encourages further research into less toxic perovskite materials, paving the way for the exploration of new compounds that can offer better performance, less environmental impact, and lower production costs.
Also read
- KIER, Flexell Partner on Next-Gen Space Solar Cells
- Fraunhofer ISE Unveils LED Method To Calibrate Tandem Solar Modules
- Researchers unveil tougher perovskite glass brick for solar façades applications
- FTC Solar Launches Hurricane-Resistant Solar Tracker System
- Study flags “no-clean” flux as TOPCon corrosion risk under damp heat
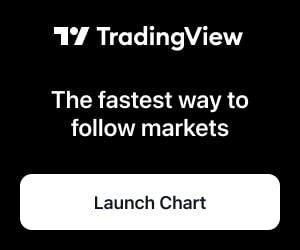