Battery Pack Prices Cited Below $100/kWh for the First Time in 2020, While Market Average Sits at $137/kWh.
- Lithium-ion battery pack costs, which were above $1,100 per kilowatt-hour in 2010, have actually dropped 89% in actual terms to $137/kWh in 2020. By 2023, average costs will certainly be close to $100/kWh, according to the current projection from research company BloombergNEF (BNEF).
For the very first time, battery pack prices of less than $100/kWh have actually been reported. These were for batteries in e-buses in China. While these were the lowest reported price, the volume-weighted typical cost for e-buses in China was somewhat greater, $105/kWh.
Battery electrical automobile (BEV) pack prices are $126/kWh on a volume-weighted average basis. At the cell degree, average BEV costs were simply $100/kWh. This suggests that generally, the battery pack section of the overall rate make up 21%.
BNEF's 2020 Battery Price Survey, which takes into consideration traveler EVs, e-buses, industrial EVs and stationary storage space, predicts that by 2023 average pack rates will be $101/kWh. It is at around this price factor that car manufacturers need to have the ability to produce and also sell mass market EVs at the exact same cost (and also with the very same margin) as comparable interior combustion cars in some markets. This assumes no subsidies are offered, but actual pricing techniques will differ by automaker and also location.
Rate decreases in 2020 are thanks to raising order sizes, development in BEV sales and the intro of brand-new pack layouts. New cathode chemistries and falling production costs will drive prices down in the near term. The prices of cathode products have fallen considering that getting to a high in spring 2018, discovering a much more steady degree during 2020.
James Frith, BNEF's head of power storage space research study as well as lead author of the report, said: "It is a historic turning point to see pack prices of less than $100/kWh reported. Within just a few years we will see the ordinary rate in the market pass this point. What's even more, our evaluation reveals that even if costs for raw materials were to go back to the highs seen in 2018, it would only postpone typical costs reaching $100/kWh by 2 years-- rather than totally derailing the market. The sector is coming to be increasingly resilient to altering basic material prices, with leading battery suppliers moving up the value chain as well as investing in cathode manufacturing or even mines.".
Leading battery makers are currently enjoying gross margins of up to 20% and also their plants are running at utilization rates over 85%. Maintaining high application prices is vital to lowering cell and also pack rates. If use prices are reduced, then tools and structure depreciation costs are topped fewer kilowatt-hours of manufactured cells.
Daixin Li, a senior energy storage space partner at BNEF, included: "The increasingly diversified chemistries used in the marketplace cause a large range of rates. Battery suppliers are competing to mass-produce higher energy-density batteries with some new chemistries such as lithium nickel manganese cobalt oxide-- NMC (9.5.5)-- and also lithium nickel manganese cobalt aluminum oxide-- NMCA-- readied to be mass-produced as early as 2021. Lithium iron phosphate-- LFP-- nevertheless plays as a cost-competitive choice, adding to the lowest reported cell rates of $80/kWh.".
The path to accomplishing $101/kWh by 2023 looks clear, even if there will definitely be missteps, such as asset cost boosts, in the process. There is much less assurance on just how the industry will certainly lower costs even better from $100/kWh to our expectation of $58/kWh by 2030. This is not since it is impossible yet instead that there are several options and paths that could be taken.
One feasible path to attaining these lower rates is the fostering of solid-state batteries. BloombergNEF expects that these cells could be manufactured at 40% of the price of current lithium-ion batteries, when generated at scale. These decreases would come from savings in the expense of materials as well as in the cost of production, equipment, and also the adoption of new high-energy density cathodes. In order to realize these minimized costs, the supply chain for vital products, such as strong electrolytes, not used in lithium-ion batteries today, requires to be developed.
Also read
- UK planning approvals for renewables smash records as storage surges
- U.S. solar build stays on record pace despite policy crosswinds
- Malaysia's Solar Ambition: 3 GW Storage Partnership
- Energy Vault And Astor Enerji Strike Cross-Supply Battery Partnership Deal
- United States Set To Add Thirty-Three Gigawatts Of Solar Capacity
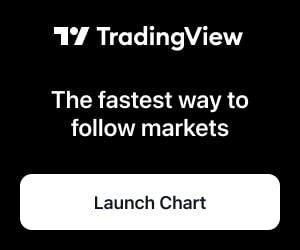