Value of local manufacturing demonstrated, utilization up but still a long way to go
Sep 12, 2019 09:25 PM ET
- Indian module manufacturers are gearing up for an end-of-year surge in solar project procurement and hoping their investments in incorporating global manufacturing benchmarks will translate into enhanced sales.
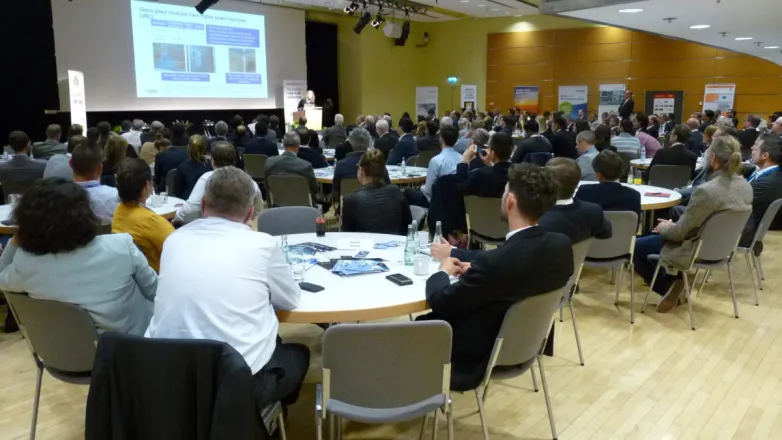
Rajaram Pai, DuPont Photovoltaic Solutions’ business leader for South Asia and the ASEAN region, says developers; engineering, procurement and construction companies; and investors are reporting higher confidence in Indian-made modules than in previous years.
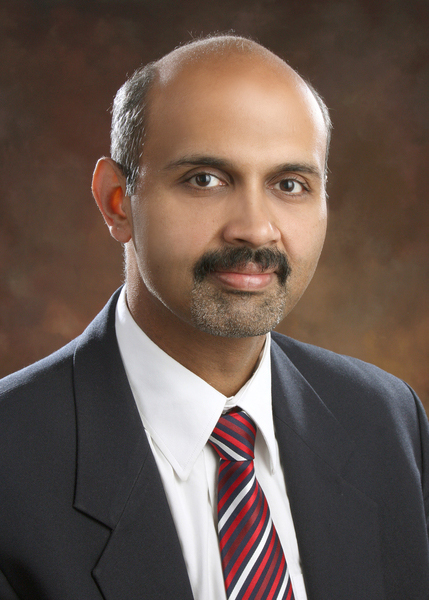
Rajaram Pai, DuPont Photovoltaic Solutions’ business leader for South Asia and the ASEAN region.
“Many developers now feel comfortable to lock in some of their requirements from the domestic sources,” DuPont’s Pai told pv magazine. “Besides the obvious external reasons – safeguard duties and fluctuating currencies, for instance – and the logistical advantages arising from local procurement driving the change; domestic manufacturers are also focused on selection of proven materials and technology, upgrading manufacturing processes and upskilling their technical resources for achieving sustained, long term performance.
“Until a few years ago there was a significant disparity in power outputs, technologies and quality between the Indian and imported modules. However, of late that gap has narrowed with enhanced in-line automated quality interventions and investments in reliability testing capabilities [that] have implied that the Indian producers are increasing their share in local PV projects.”
Developers are selecting a “blend” of locally produced and imported modules for projects, said the DuPont rep.
BIS steps in
On the policy level, the development and application of Bureau of Indian Standards (BIS) benchmarks to solar PV manufacturing and testing has played a role in boosting standardization on Indian production lines. One positive aspect, said DuPont’s Pai, is that it has made manufacturers stay consistent with a certified bill of materials, owing to higher switching-related certification costs. “It has also deterred companies supplying sub-grade material to a large extent,” added Pai.
However, there is still room for BIS to comprehensively integrate the nuances of harsh Indian environmental conditions beyond the existing regulations. Engineers from German testing institute PI Berlin recently noted that while environmental conditions such as salinity or high UV, humidity, heat, sand or strong winds are often experienced by global PV project developers, “in several areas of India, PV projects often face several … of these factors at the same time”.
There is also a need, said Pai, to establish more testing facilities to carry out BIS accreditation. He noted there are numerous “prestigious scientific institutes in the country that can be integrated into the testing and certification framework that could carry out such testing”. Expanding the number of such testing facilities, Pai said, could accelerate the certification process for new material.
MAST testing
In terms of testing, DuPont continues to advocate for the more widespread adoption of Module Accelerated Sequential Testing (MAST) in India and elsewhere. Pai said the company continues to work with private and government agencies for the adoption of the MAST regime.
MAST involves sequential testing of PV modules to apply humidity, thermal and UV stresses on materials – pushing them to their limits. DuPont suggests the regime more accurately replicates real world conditions, particularly in countries such as India where high levels of humidity, high temperatures and abundant UV are present.
“The realization is coming that there is a high correlation on what the module will actually look … or behave [like] in the field to what it undergoes in the actual [MAST] test scenario,” said Pai. “It won’t happen overnight, in terms of switching from the IEC [International Electrotechnical Commission] requirement, but … people want to ensure that the materials are robust and have been proven to perform in the field for their intended lifetime.”
DuPont has said the PV installation run rate in India has been slow this year due to tender challenges, late payments from power distribution companies and other regulatory uncertainties. But the manufacturer expects installations to pick up sharply towards the end of the year, and in 2020. “Q4 of this year and Q1 2020 will be an intense period of installations,” added Pai.
Also read
- Boviet Solar Completes 3-GW Factory Exterior in North Carolina
- China industry profits sag as solar overcapacity strains manufacturers nationwide
- Despite turbulence, US solar manufacturing expands domestic supply chain plans
- China’s Solar Makers Signal Progress Amid Losses And Overcapacity Shakeout
- China’s industry group tells solar makers: stop below-cost price wars
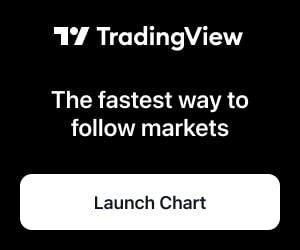