Types of solar panels and how they are manufactured?
- There are many types of solar panels and in them silicon ones make to the top of the list. They are evolving with time and getting cheaper with the economy of scale.
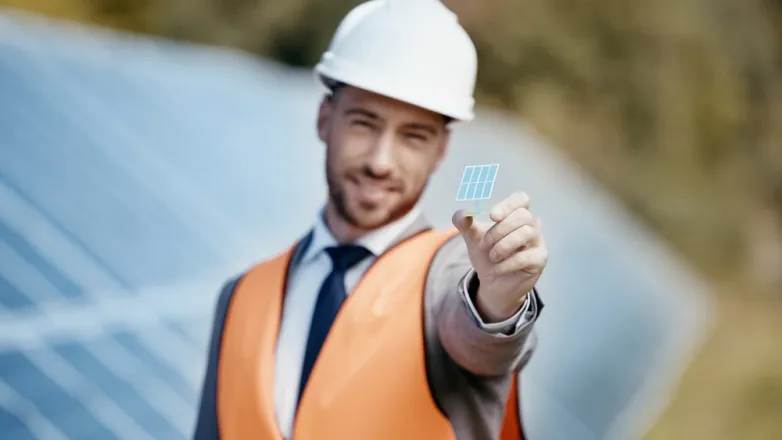
The use of solar energy is increasing day by day. Subsequently, there are many companies selling many types of solar products, each with a solar panel. Like there are small solar panels on calculators and gadgets and even big ones on roofs or ground. However, all the different types of solar panels do the same thing of absorbing sunlight. They all produce current for our use in one way or the other. We all know there are different ways to make use of solar panels in our daily lives.
It is different to use a gadget and understand it fully. However, if we understand the technology well, we know how we can use it well. Indeed the understanding the composition of solar cell makes it easier to understand how it works. Basically, the photons of light from the sun, transfer their energy to electrons in the solar cell. This happens at the p-n junction of the solar cell or the positive and negative junction of semiconductor like silicon etc. The semiconductor should have enough energy band gap to make the electrons jump and generate current.
As solar panels constitute of a number of solar cells. Similarly, semiconductors like Silicon and others around silicon in the periodic table make the core of a solar cell. To make a solar cell there are different materials and techniques. Let us have a look at a list of these materials with their energy band gap in eV. Here, eV is Electornvolt a unit of Kinetic Energy.
Also see: Solar Panel Manufacturers and Suppliers Directory
Types of semiconductors and other materials
- Elements
- Silicon 1.12 eV
- Germanium 0.67 eV
- Compounds
- Gallium arsenide 1.42 eV
- Indium phosphide 1.34 eV
- Gallium antimonide 0.7 eV
- Copper indium diselenide (CIS) 1.0 eV
- Cadmium telluride (CdTe) 1.5 eV
- Copper indium gallium diselenide (CIGS) 1.3eV
- Cadmium sulphide 2.42 eV
- Zinc sulphide 3.6 eV
- Lead sulphide 0.37 eV
- Tin sulphide 1.35 eV
- Copper indium disulphide (CuInS2) 1.5 eV
- Others
- Perovskite 1.48-1.62 eV
- Organic NA
- Quantum dots NA
So that is an extensive list of semiconductor material but it narrows down with the important ones. Certainly, silicon is used in few different ways to make solar cells. Also, they are efficient and cheap at the same time, due to abundance of silicon. Other compounds like CIGS, CIS, CdTe and CuInS2 are also used to make solar cells and panels but in limited way. Whereas, perovskite, organic and quantum dots technologies are under research with possible potential for the future. Furthermore, let us have a look at the types of solar panels which are available in the market.
Types of Solar Panels
- Mono-crystalline silicon
- Poly-crystalline silicon
- Thin Film
These are the main types of solar panels which are available everywhere. Silicon alone takes more than 95% of market share in the solar panel market. So let us have a look in brief on what these types of panels are before we dive on how they are manufactured.
Mono-crystalline solar panels
These panels are composed of mono-crystalline solar cells, also known as single silicon crystal cell. It is easy to identify these panels with dark black cells in a grid formation. The cells have cut edges to give an octagon shape. In initial days round mono-crystalline cells were used in panels which wasted lots of panel space. However, these are the most efficient solar panels because they are made from pure silicon.
With average energy output efficiency of 20% and even more. These solar panels are also the most space efficient among all other types of solar panels. Not only these solar panels are the efficient but also the oldest form of solar energy technology. Also, these solar panels have guaranteed working life of 25 years and are able to generate electricity for more than 50 years.
Due to heavy manufacturing costs, these solar panels are the costliest among all. However, the highest energy output with more technologies like PERC & PERT etc are making them more economically viable.
Poly-crystalline solar panels
Unlike mono-crystalline with single silicon crystal structure. Poly-crystalline silicon also known as multi-crystalline silicon constitute many silicon crystals. These panels give a blue hue in color and has mosaic like pattern at front. The cells have a square shape with no wastage of silicon in making. But, the efficiency of poly-crystalline silicon is quite less than the mono ones because of many silicon cells.
The main benefit of these poly-crystalline solar panels is their low prices. The easy process of manufacturing these cells make them about 20% less expensive than mono-crystalline solar cells. The manufacturers of these solar panels give working life guarantee of 25 years.
Due to their low costs and good efficiency of around 15% and even more. They are a choice for large scale and small scale power plants alike. Addition of new technologies like PERC, PERT and HJT are making them more efficient in power production.
Thin film solar panels
As the name suggests, these solar panels are thin in structure. There are different types of thin film solar panels. Different materials used make different thin film solar panels. Like,
- Amorphous silicon
- Cadmium telluride (CdTe)
- Copper indium gallium selenide (CIGS)
Among these Amorphous silicon thin film is most popular. Also, multi junction amorphous silicon is preferred for its flexibility better performance and lower degradation with time. Drawback with amorphous silicon is its less energy output efficiency.
Their flexibility and high efficiency of energy conversion promote CdTe and CIGS solar cells. Almost 17% for CdTe and more than 20% for CIGS solar panels is the average energy output efficiency. These solar cells have promising future because of lower costs of production than silicon solar cells.
How solar panels are manufactured?
As discussed there is number of materials which are available for solar cell manufacturing. Also, only a few are available in the market, depending on their usage viability.
Let us have a look at manufacturing process of main types of solar panels to understand them more.
Manufacturing of mono-crystalline silicon solar modules
These solar panels have pure silicon in them. The manufacturing process from silica to mono-crystalline solar modules consist of following steps:
Purification, distillation and refining
- SiO2 or Silica is the raw-material to make silicon. It is available in abundance as on Earth oxygen and silicon are two most abundant elements. Quartz is the natural source of silica. Also, it exists in many parts of the world. The first step is to make metallurgical grade silicon from silica. This happens in an arc furnace with temperature ranging till 2000 deg C. In the furnace silica is purified with coke. At the end of the coke reduction reaction we get metallurgical grade silicon.
- In the second step, with the use of hydrochloric acid or HCl and after dissolving metallurgical grade silicon in HCl. We get chlorosilanes in the end.
- Fractional distillation is the third step. Here high purity trichlorosilanes are the end product after distillation of chlorosilanes.
- In the fourth stepp we get poly-crystalline silicon from trichlorosilanes. This happens after reduction reaction of trichlorosilanes at 900 deg C in presence of Hydrogen.
Czochralski process
- · Czochralski process, the fifth step is the most crucial step to make mono-crystalline silicon. With Czochralski process formation of single crystal silicon happens. Firstly, by adding impurities to the molten silicon like boron and phosphorous, the silicon becomes either n-type or p-type silicon. Also, the temperature of the molten silicon in the crucible is about 1415 deg C. Next, dipping single silicon crystal molten silicon is the turnaround moment. The silicon crystal starts the crystal growth as it moves up with rotation. At last a single silicon crystal or Ingot comes out of the crucible. This silicon ingot is about 1 to 2 meters in height.
Cutting, washing and doping
- In the sixth step with the help of diamond saw, silicon in wafer form is available from Ingot. The sawing of Ingot in a precise manner makes octagon shape silicon wafers.
- Then in the seventh step mechanical and chemical washing of silicon wafers happens. Subsequently, polished silicon wafers are available.
- The eighth step is also important where p-n junction comes into form. The p-n junction making process involves adding impurity to the wafers. For N-type silicon wafers, boron doping makes the p-n junction or p on n device. Similarly for p-type silicon wafers, phosphorous makes the n-p junction or n on p device.
- In the ninth step, anti-reflection coating with materials like silicon nitride makes it ready for connections.
Interconnection, encapsulation and module assembly
- Formation of front contacts happen in the tenth step. Super conductive metals like silver makes the front contact. Either screen printing or burying of contacts makes the solar cell ready to encapsulate.
- In the eleventh step, interconnection of solar cells to each other with encapsulation and assembly in module takes place.
In this way mono-crystalline solar panels come into existence.
Manufacturing of poly-crystalline silicon solar modules
These solar panels have multi-crystalline silicon solar cells in them. The first four steps are the same as that of mono-crystalline solar panel manufacturing. This means that purification, distillation and refining are same for both mono and poly.
After poly-crystalline silicon is available after refining. Impurities same as boron or phosphorous make the silicon n-type or p-type. The molten impure silicon is then poured in square moulds. Later after cooling of these square moulds, cubic ingots of poly-crystalline silicon are taken out.
Further, process is the same as that of mono-crystalline silicon panels. From cutting, washing, doping to interconnection encapsulation and module assembly. All the processes replicate except the ingot formation.
Manufacturing of thin-film solar modules
There are different thin-film solar panels and their manufacturing is different. We can have a look at their manufacturing process one by one:
Manufacturing of amorphous silicon modules
These solar cells have distributed arrangement of silicon cells. Or to say, these cells have random arrangement of silicon atoms. Here, chemical vapur deposition or CVD process makes these cells. Specifically, Plasma Enhanced CVD of gases carrying SiH4 or silane is done on a substrate like aluminium. Finally, the deposit is an alloy containing silicon and hydrogen.
The structure of amorphous silicon is p-i-n or n-i-p where "n" and "p" are the negative and positive layers of silicon. "i" is the electric field which forms between these n & p layers. Amorphous solar cells which have multi-junction layers are more efficient. The layers are very thin so the flexibility in these cells.
Manufacturing of CdTe solar modules
These are also thin film solar panels like amorphous silicon but the deposition of semiconductors is not the same. The structure of CdTe solar cells is p-n heterojunction. In this case, the CdTe layer is p-type with cadmium sulphide (CdS) top layer as n-type. For this cell thin film deposition techniques like thermal evaporation, sputtering and electrodeposition are used.
Manufacturing of CIGS solar modules
Copper Indium Gallium Diselenide or CIGS solar cells also use deposition techniques. These deposition techniques are:
- Co-evaporation method in which elements sublimate in high vacuum and deposit again on the substrate.
- Annealing of pre-sputtered metal layers in environment of selenium.
The deposition of CIGS layer is done by the techniques mentioned above. Deposition of n-type CdS (Cadmium Sulphide) is done by chemical bath on CIGS layer. Later Zinc oxide with high resistance and a n-type highly conductive Zinc oxide layers are depositied with sputtering. With laser scribing technique during the process, individual solar cells connect each other.
Conclusion
The main types of solar panels like mono-crystalline and poly-crystalline are mature technologies. Their manufacturing processes are also mature. New developments are popping up to increase the efficiency of these solar panels. Technologies like PERT (Passive Emitter Rear Totally Diffused), PERC (Passive Emitter Rear Contact), HJT (Heterojunction) and bi-facial solar panels all increase efficiency of mono-crystalline and poly-crystalline panels alike. Similarly, other types of solar technologies like perovskite, organic and quantum dots also are expected to make some mark in the future.
Also read
- Exploring the Key Players in Dubai’s Solar Panel Distribution Market
- Solar Site Selection: How to View Historical Satellite Images To Track Land Changes Over Time
- SEF 2025 Kyiv: Forum on Innovation and the Restoration of Ukraine’s Energy Sector
- Innovation and Sustainability Arrive in Bucharest at the Country’s Largest Exhibition for Green Technologies and Solutions
- Energy risk management: How businesses can protect themselves from market volatility
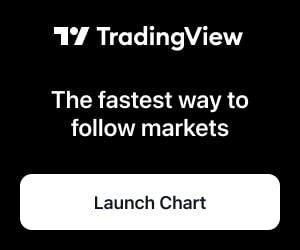