The weekend read: Next steps for HJT
Oct 15, 2019 10:03 PM ET
- There is movement in the heterojunction space, but will it be enough to surpass PERC’s momentum? New production lines show promise, but they might also be the last roll of the dice for Swiss production equipment supplier Meyer Burger.
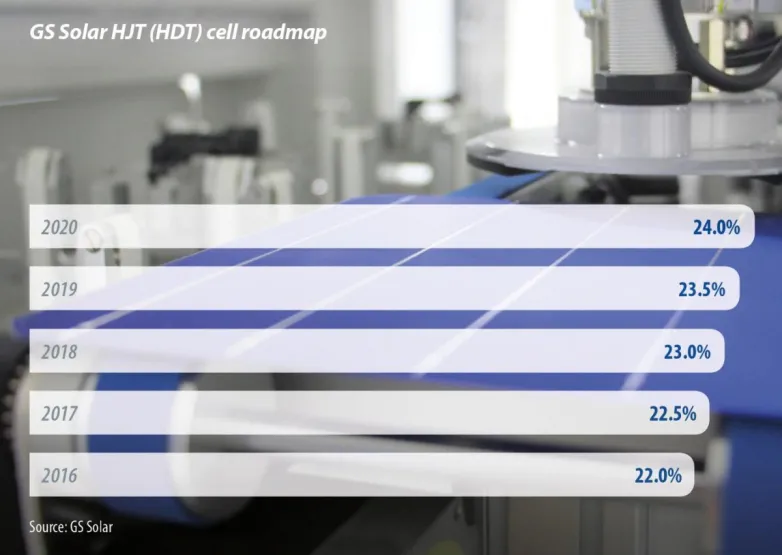
It is considered conventional wisdom among some in the PV production community that for technology upgrades, PERC including TOPCon is the obvious choice, while for greenfield projects, the only way is heterojunction (HJT). But as the 2019 PV market heads toward its final quarter, it remains unclear whether this technology dynamic is self evident.
One major development on the HJT front in 2019 has been REC Group’s embrace of the technology. At Intersolar Europe in May, REC launched its new Alpha Series HJT module with 380 W of output in a 60-cell configuration. Alpha deploys Meyer Burger HJT deposition and Smartwire cell interconnection technology. On release, module efficiency came in at 21.7% and 21.4% for an all-black module.
REC dove headfirst into HJT, particularly from a volume perspective as a non-Chinese manufacturer. In one fell swoop, it purchased 600 MW of HJT production equipment – and it is currently ramping that up further. First shipments are expected in October and November to Europe, the United States and Australia.
“There were very interesting reactions from people,” says REC Group CTO Shankar G. Sridhara. “They have been surprised because it is a bold move jumping to HJT and it is also very bold doing 600 MW in one shot. But we are confident about the due diligence that we did and the module development that we did on the side.”
The Alpha modules combine HJT and advanced connection technology with REC’s “Twin Panel” design, which the company pioneered back in 2014, along with half cut cells.
Sridhara sets out the thinking behind the move: “REC with its size of around 1.8 GW can’t compete on the standard technology, which is now PERC. With the n-PERT which we launched last year, we are ahead, but in order for us to be a true technology leader, we have to maintain a significantly larger distance to our competitors. HJT is the right technology to do that, both from a performance and, naturally in this industry, from a cost perspective.”
Cost in focus
In terms of costs, there are concerns that the capex requirements for investments in new HJT lines remain too high. Ethan S. Simon, the CTO of DuPont Photovoltaic and Advanced Materials, says that production equipment capex for an HJT line may be up to two times higher than for a standard mono PERC line. However, he notes that efforts to advance large area PECVD equipment could reduce that margin significantly. “The investment required could be a damping factor,“ says Simon.
PV InfoLink analyst Corrine Lin estimates that HJT capex, drawing on Chinese equipment supplier figures, is around CNY 0.75-0.85 billion ($100-120 million) for 1 GW of capacity, with PERC coming in at around CNY 0.25 billion.
On the opex side, too, there are challenges. Early HJT cells were sometimes described as being heavy on the silver paste laydown for cell metallization, although here progress has been made. “Our fourth-generation [HJT paste] version reduces the cost of the process by offering up to one-third reduction in paste usage,” says DuPont’s Simon.
But indium, often used for the transparent conductive oxide (TCO) layer, does not come cheap – particularly if large volumes have to be purchased at the start of production. Indium tin oxide is favored for the TCO in HJT production.
Technological inertia
A further limiting factor for HJT adoption could simply be technological inertia, as PERC is well established and understood by manufacturers and the market, now that it has gone through a long gestation period. “They have done their homework on PERC and now they have to think what’s next,” says Christian Knechtel, the CEO and CFO of German production equipment supplier Von Ardenne. In PV, Von Ardenne supplies coating equipment to the thin-film segment – First Solar being a notable client, along with TOPCon and HJT crystalline silicon manufacturers – specifically for physical vapor deposition (PVD) of the TCO layer.
“We also see a lot of people understand PERC and its efficiency restrictions, which could be eliminated by TOPCon. People are a bit reluctant when it comes to technology change,” says Knechtel. This reluctance may be more pronounced given the strong efficiency gains made by PERC producers, in its various flavors.
Oliver Voigt of wet chemical equipment supplier RCT Solutions asks: “If TOPCon cell efficiency of 22.5% can be achieved, then why would you go to HJT?”
24% and beyond
The promise of a potential 24% cell efficiency in mass production is what makes HJT production so enticing, along with the relative simplicity in terms of process steps. REC is an experienced PV producer and with 600 MW running at high utilization rates, presumably learnings will be accelerated. And beyond REC, there are moves by other tier-one manufacturers into HJT.
In August, Risen Energy broke ground on a 2.5 GW HJT cell and module facility in China’s Zhejiang province. The company plans to invest some CNY 3.3 billion in the facility. Risen Energy says HJT’s advantages are its good temperature coefficient, along with its resilience to “light and power degradation” – presumably LID and LeTID. Zengsheng Liu, director of module R&D for Risen, adds that HJT exhibits up to 90% bifacality – far superior to that achieved by PERC or PERT.
GS Solar, a production equipment supplier based in China’s Fujian province, claims to operate 1 GW of HJT capacity, which it calls HDT technology. The company’s core technological competence is in PECVD and PVD technology. But PVInfoLink’s Lin says that the company pivoted from HJT equipment supply to cell and module production after experiencing limited demand for its equipment.
In May, HJT pioneer Panasonic transferred the ownership of its Malaysian HJT manufacturing facilities to GS Solar and launched a joint venture for ongoing R&D. The partnership aims to “drive further development of heterojunction photovoltaic technologies,” according to a statement by Panasonic – presumably with cost reductions front and center.
Veteran solar analyst Götz Fischbeck, from Smart Solar Consulting, believes that while recent HJT deployments are encouraging, there are still considerable headwinds for the technology – most notably the capex requirements. Fischbeck understands the Meyer Burger/REC deal includes some form of profit sharing and a period of “technological exclusivity” for REC. For the Swiss technology provider, Fischbeck believes, it also “represents the last chance for Meyer Burger to survive as an equipment supplier to the solar industry.”
Also read
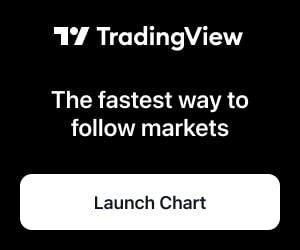