The weekend read: Perovskites step out of the labs
Aug 12, 2019 10:20 PM ET
- Michael van der Gugten, Sales and Marketing Executive at Smit Thermal Solutions, is convinced that perovskite solar cells have reached maturity, and that they are ready to make the step from the lab to production. He is leading the organization of a conference on this topic and expects that the perovskite community, production equipment suppliers and crystalline silicon cell manufacturers will discuss the implementation of perovskite-silicon tandem cells or the production of standalone perovskite modules.
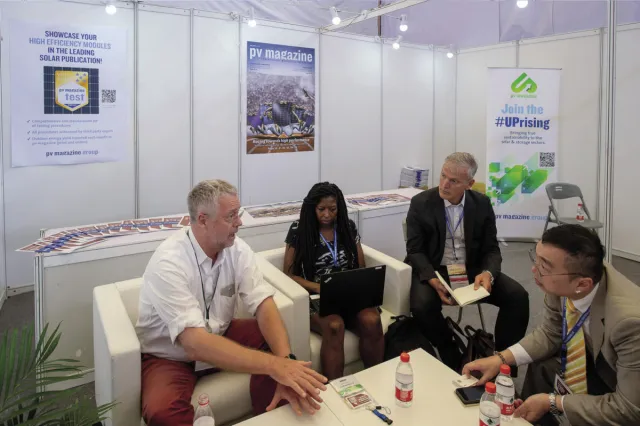
You have been developing production equipment for organic PV and thin film manufacturing for several years, and now you say it’s time to adapt it to perovskite production. What makes you believe that perovskites will be a success?
Perovskite solar cell development started 10 years ago and in a short time we saw very large improvements in efficiency. In the last two or three years we also saw an improvement in durability. We focus on companies who are active in the thin film market and build pilot and mass-production equipment, as perovskites belong to the group of thin film technologies. We were involved in pilot line development for companies active in organic (OPV) and, later on, also in the field of perovskites. These systems are in use, for example, at an institute in Eindhoven called Solliance. They have a roll-to-roll dryer system built by Smit. It was used for OPV and is now used for the development of perovskites. Also we delivered a spatial ALD [atomic layer deposition] system.
When will there be a perovskite cell or module that is established — one that is not solely used for R&D and that people can buy?
I strongly believe that within two years the first large-scale panels, be it as a tandem or as a module layer, will enter the market. The developers are already looking at this and are waiting for mass production solutions already.
But I also see that researchers are still looking for materials and encapsulation technologies to make the perovskites stable enough, and to reach high efficiency at the same time. Do you think the development of production tools, lines and this research should go on in parallel?
Yes, partly it will go in parallel. But there are also companies that already have a running process with quite impressive efficiencies. They are at this moment really focusing on this mass production.
That is why you are organizing a conference on this topic on October. In terms of production equipment for the perovskite layers, you offer two technologies: vacuum deposition technologies and tools for solution-based applications, such as slot die coating and inkjet printing. Which is the most promising in terms of efficiency and costs?
This is really an open question. At this moment you see people working on solution-based techniques on quite large substrates and you see people who use vacuum technology with different kinds of deposition techniques, among which you find evaporation technologies. Who will be the winner? I don’t know, it depends on the success of the technologies with regard to durability and efficiency. There will be different companies that offer production tools — for example, the company nTact with their solution for slot die coating.
What are the challenges?
The big challenge for perovskites is the durability. Degradation is caused by moisture and encapsulation is key. We can contribute to solutions, for example, with our ALD technology. With this you can create an aluminum oxide layer that you can use as an encapsulant. As we are not involved in process development itself, I’m not the best to answer about all the most relevant challenges. But if we look to machinery, we have some solutions for different challenges caused by moisture. Low-temperature processing using a combination of ALD with a plasma especially benefits the perovskite processing.
To avoid misunderstandings: For most people in the crystalline community, encapsulation means that you use EVA sheets to protect cells. But when you’re talking about encapsulation, you use layers that are directly deposited on the cells. To come to the similarities with thin film technologies — you say that you have supplied tools for over 5 GW of thin film production capacity. Which of these technologies is closest to perovskites?
That is difficult to say. You have similarities across the whole group of thin film technologies. For OPV you also use dryer solutions, which you need for solution-based application of perovskites. There are even similarities with CIGS and CdTe deposition solutions in terms of the vacuum deposition technology.
In crystalline silicon cell production, one uses ALD, vacuum technology and PECVD for some specific layers. Why can one not just use the same tools?
In perovskite production you have to consider that the temperatures need to remain below 150 degrees. In crystalline production this is not important. So you have to look for different production approaches, and that is where we are strong. Our basic technology relates to temperature control and we combine that with our vacuum systems and plasma options, and with ALD. In this way we can implement a low-temperature aluminum oxide deposition. We can even stay below 100 degrees.
How are you doing this?
In spatial ALD you first apply one precursor and then you move your substrate to the next slot for the second precursor. For one of the precursors you use a plasma to break up chemical bonds. By this plasma enhancement you lower the temperature.
And what is your USP in the market for tools for thin film?
We spent time to find the companies and the institutes that want to go into pilot production. We want to accompany the companies in developing the pilot lines, invest in R&D and build up our experience. The step from laboratory into mass production will happen in the coming one and a half years. At the beginning, this will be done only by a few companies. But after this has happened, the market will grow and will be interesting for many players.
Production involves not only the deposition of the perovskite and encapsulation layers, but also that of electron and hole transport layers, which connect to the perovskite. Is it also possible to deposit them using your tools?
For ETL and HTL layers it would be possible to deposit tin oxide, titanium oxide or nickel oxide. You can do it with plasma-enhanced ALD, but we have to investigate and discuss with the manufacturers if this is the right process approach. There is not yet a standard in perovskite production and the manufacturers have to decide which technologies they want to use.
Will this be one of the hot discussion topics at the conference?
Yes. There will be institutes that already run pilot production with strong views on how to set up mass production. They have ideas about how to produce large quantities of perovskite material and how to design any kind of modules. There will also be companies who start mass production and will give an overview on what they are doing.
What is the situation with experts in crystalline silicon production — are they already interested in this topic because they might think about using silicon-perovskite tandem technology?
Yes, they are. One of the invited speakers is Chris Case from Oxford PV. They invested in a production facility for tandem technology in Brandenburg, close to Berlin. The crystalline community is interested in this topic.
What is the situation with Chinese crystalline manufacturers?
They are in discussions with our customers. We know that most of the cell and module manufacturers are interested in perovskite development. GCL, for example, will also be at the conference. They have their own perovskite program.
What other highlights can participants expect?
The company Microquanta will present their ideas. It is a Chinese company from Hangzhou. They have R&D/pilot production for perovskites. The results they communicate are really impressive.
How many participants do you expect?
We expect between 150 and 200 people at the conference. The program is already fixed and available online.
Also read
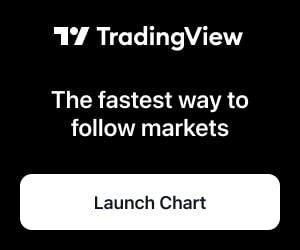