Risk management in manufacturing plants: strategies for mitigating operational challenges
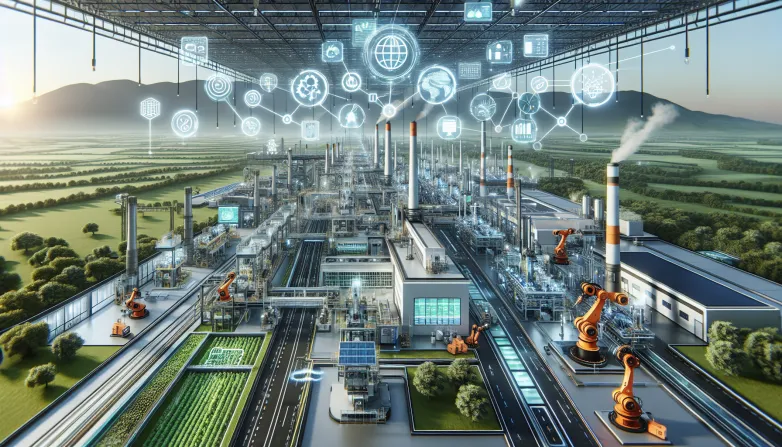
Imagine a world where every manufacturing plant operates with the precision and predictability of a well-oiled machine – no breakdowns, no miscommunication, just seamless production. Implementing a robust plant process management solution makes this scenario closer to reality than you might think.
Enter the realm of risk management, a critical consideration if you're navigating the complex terrain of modern manufacturing. It's not just about preventing problems; it's about creating a robust and agile system in the face of operational challenges.
Integrating digital solutions for enhanced coordination
One of the keystones in today's risk management is incorporating digital solutions that simplify process monitoring. A prime example is the use of a plant process management solution that can streamline the way information is communicated across shifts. Picture a scenario where the outgoing team records their insights into a digital log and the incoming team can instantly access this information, ensuring a seamless transition. Real-time updates keep everyone on the same page, reducing the chance of errors and downtime.
Moreover, the digital era has made it possible to implement advanced monitoring systems that track the health of machinery in real-time. Sensors and IoT devices collect data that can be analyzed to predict equipment failure and necessary maintenance. This constant monitoring ensures that potential issues are identified before they lead to costly downtime, making operations more efficient and reducing the risk of unexpected interruptions in the production process.
Advancing proactive risk assessment
Waiting for something to go wrong before you address it is like closing the barn door after the horse has bolted. Smart manufacturers know that danger lurks in complacency, so they're always on the lookout for potential issues.
This might mean regular equipment audits or predictive analytics that can foretell a problem before it erupts. By taking a proactive approach to risk mitigation, plants can stay one step ahead and ensure smoother, safer operations.
Merging sustainability with operational viability
As the sun powers solar panels, sustainability drives modern manufacturing resilience. Factories that harness renewable energy reduce their ecological footprint and shield themselves against energy supply fluctuations. Sustainable practices also resonate well with an increasingly eco-conscious market, providing a competitive edge.
By integrating green principles into every facet of operation, a manufacturing plant contributes to a better planet. It builds a foundation of trust with its customers and partners.
Optimizing crisis management through tech
No one likes to think about emergencies, but the best time to prepare for a storm is when the skies are clear. Advanced technology plays a critical role here. Data analytics can provide insights that enable quick, informed decisions amidst disruption.
Furthermore, a robust, tech-driven crisis management plan often includes backup systems that keep the plant humming even when primary systems falter, demonstrating the importance of resilience and the ability to bounce back swiftly and efficiently.
Fostering cross-functional teamwork
The adage "two heads are better than one" aptly applies to risk management in manufacturing. When communication silos crumble and departments work together, the results can be transformative. Consider a scenario where the maintenance and production teams collaborate closely, using technology to flag issues before they escalate. This teamwork can fortify a plant against challenges, fostering a shared responsibility and collective problem-solving culture. Transparency mitigates risks. It empowers every stakeholder with a sense of ownership and a vested interest in the plant's success.
In summary, tackling operational challenges in manufacturing is an ongoing exercise in vigilance, innovation and collaboration. From digital shift logs to sustainability, the strategies discussed offer a roadmap for plants aiming to thrive in an environment fraught with potential risks. By embracing these methods, manufacturers can look forward to surviving operational hurdles and mastering them, turning their plants into ideals of efficiency and reliability.
Also read
- How to Get Better at Writing This Summer: 5 Tips to Build Your Skills
- WriteMyEssay Review: Discover Why It’s Among the Best Websites That Write Essays for You
- Solar Site Selection: How to View Historical Satellite Images To Track Land Changes Over Time
- Upgrading Your Home: Tips for Maximizing Value and Enjoyment
- Revolution Beneath the Streets: Smarter Solutions for Underground Infrastructure Rehabilitation
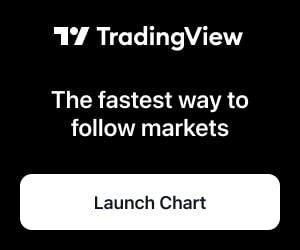