Heat storage in solar plants
- Tim Bruewer information optimum thermal management for using molten salt in solar thermal nuclear power plant with focused radiation
The demand for eco-friendly and also low-CO2 kinds of energy generation has actually been raising in Europe since the 'Green Deal' existed by the EU Commission in 2019, specifying the environment nonpartisanship of 26 member mentions approximately the year 2050. To name a few methods, the focus gets on solar energy as a vital representative in this area.
Solar thermal power plants with focused solar power (CSP), particularly, commonly offer higher performance than solar systems. To make up for the rising and fall manufacturing of power due to altering solar radiation, molten salt is usually made use of for warm storage space in such plants. Nevertheless, if the temperature level of the thaw drops below a limit of around 228 ° C, conventional salt substances "freeze," which can obstruct lines. On the other hand, if the temperature is expensive, at around 585 ° C, the salt liquifies and also can no longer be made use of as a heat carrier. Additionally, leak can take place at the valves, minimizing efficiency as well as enhancing the chance that the thaw will certainly ice up. As a result, comprehensive warm management is required to guarantee that the temperature of the salt is secure. This can be achieved by a heater containing electrical home heating modules, sensing units, and also control units to secure the temperature level of the molten salt at any type of factor in the plant.
Over the last few years, social and political activities have actually led to a raised concentrate on sustainable types of energy in the nations of the European Union. According to information from the Energy Industries Council (EIC), a lot more renewable resource jobs are presently being planned and also applied in the EU location than in any other region on the planet. The same relates to solar thermal generation with focused radiation (CSP) particularly, which, in comparison to now debatable wind energy, is characterised by particularly reduced environmental impact. The European Solar Thermal Electricity Association (ESTELA) puts the variety of continuous systems in Europe at 2,385, with a further 588 systems being planned. Spain, as an example, as the European pioneer of solar thermal energy, is working on new regulations that intends to release brand-new tasks by 2024. Nonetheless, to make this type of power generation sustainable and at the same time cost-effective, it is needed to optimize efficiency on the one hand, and also minimise disruptive factors in operation on the other.
Molten salt as common solar energy storage
A necessary beginning factor for the reliable and also cost-saving use of CSP systems is the warmth provider distributing in the system. In the example of a CSP plant utilized below, sunlight is focused by mirrors onto a main tower, which takes in the light and hence transfers the warm to a liquid power source inside the tower. Here, the tool usually made use of is molten salts, which transcend to thermal oil as a result of their homes: while the oil can be used just as much as about 400 ° C, liquified salt is secure as much as about 565 ° C. By this indicates, vapor can be generated at a higher temperature, which has a positive effect on the efficiency of the steam generator as well as hence on the energy created in the power generator. Because of this, chemical substances such as NaNO3 and KNO3, which must first be pre-heated to a temperature of about 265 ° C to be able to distribute, have actually proven themselves for a long time. After the thaw has been better heated by the solar heat in the central absorber to regarding 565 ° C, the salt initially streams right into a tank where it is kept at a continuous temperature level. Depending upon the system, it can continue to be there for several hrs in order to give warm or power during the night or throughout cloud cover. The plant then pumps the salt to a steam generator where the heat of the salt is used to generate heavy steam from water. Throughout this process, the salt cools as well as is after that fed back right into the cycle. The resulting steam in turn runs a vapor turbine as well as an electrical power generator, which ultimately produces power
Cold and also leakage are primary dangers in making use of liquified salt for solar power.
However, in this intricate process, which is qualified by very large differences in temperature level, difficulties arise that can affect both the effectiveness and the condition of the system. As the thaw makes its back to the central tower from the heavy steam generator, there is a threat that the temperature level of the salt will certainly drop listed below a particular limit of about 228 ° C, as well as the salt will certainly solidify (referred to as "cold"). This offers a fantastic threat for the plant, as the salt can block pipes as well as consequently closed down the whole procedure. At the same time, a substantial amount of energy is needed to reliquefy the solidified salt. This results in a poor power equilibrium and jeopardizes the earnings of the plant. A further risk is that leakages may occur at the valves in the pipelines utilized. This subsequently minimizes the temperature of the thaw, and the likelihood of freezing rises. The loss of salt also has a negative impact on the efficiency of the plant and also may lead to downtime if the valves need to be repaired. Extreme heating of the salt is likewise essential: if a temperature level restriction of about 585 ° C, which differs depending on the molten salt, is surpassed, the salt dissolves and also can no longer be made use of.
Temperature level management makes certain stable molten salt circulation
To counter these troubles, the temperature is continuously monitored as well as regulated by a heating unit. This requires delicate temperature sensors, which are mounted in the storage tanks in addition to in the inlet and also outlet storage tanks of the central tower. For a continuous temperature level of the melt in the tank, effective burner are likewise needed. This task is usually executed by 6 to eight immersion heating elements, which are mounted in an additional cladding tube, as well as each has a size of regarding 5m (16ft). The products made use of in the containers have to also be deterioration resistant and also suitable for high temperatures. The austenitic iron-nickel-chromium alloy Alloy 800 or the special steel SS347H, for instance, are suitable for the coverings of the heating elements. This means that temperature levels as much as 600 ° C are no worry, the product is deterioration immune and also secure even at reduced temperature levels. Additionally, components subjected to media may also be made from chrome-nickel stainless-steel AISI 347H, which likewise endures heats and also is immune to intergranular rust.
However extensive temperature management is required not just in the tank: countless temperature level sensing units as well as controllers need to be installed in the absorbing tower likewise, to make certain an attire circulation of the melt. To guarantee that the temperature level remains continuous there, all lines bring medium are fitted with high-temperature, tubular heating elements, which are characterized by a specifically short home heating time as well as are themselves warm resistant up to 982 ° C, thanks to making use of Alloy 800 or unique steel SS347H. At the same time, the temperature level of the melt can be controlled with the aid of control modern technology in such a way that no locally restricted cool zones take place. As an option, mineral-insulated cords can also be made use of to heat up the lines. In general, the warm administration system makes sure that the temperature level is kept track of without interruption, as well as therefore the molten salt can be made use of without any costly downtimes or loss of effectiveness.
Also read
- FTC Solar Launches Hurricane-Resistant Solar Tracker System
- Study flags “no-clean” flux as TOPCon corrosion risk under damp heat
- Lead-Free Solar Cells Achieve Breakthrough 33% Efficiency
- Leapting Robots Revolutionize Middle East Solar Installation
- Cosmic Veil Coating Boosts Perovskite Solar Cells for Space Missions
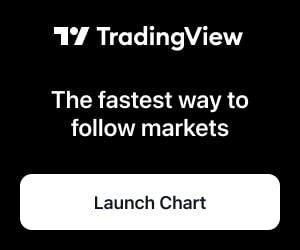