Harmful lead in photovoltaics – are there sustainable alternatives?
- Without globally unified standards in waste management, the risk from toxic materials such as lead will become increasingly important.
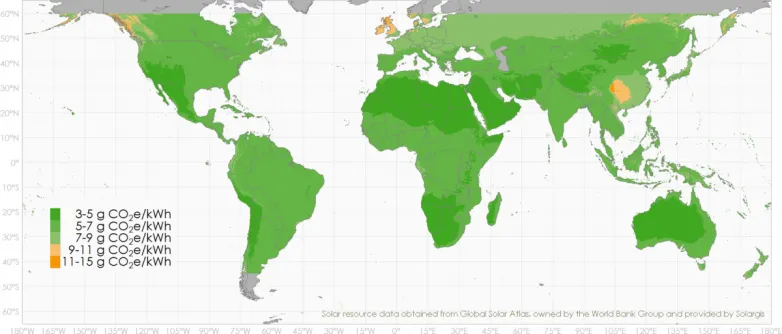
When deploying solar energy solutions, the sustainability of the products used should be an important aspect, from manufacture to use and disposal. The production of photovoltaic modules can already be questioned, because a lot of energy is needed, chemicals are used and heavy metals are still included. This can have extensive consequences, because the toxic heavy metals lead and cadmium, in particular, are used in PV modules in significant quantities: “From the installed capacity and the performance-related weight, we can estimate that in photovoltaic industry by 2016 about 11,000 tons of lead and about 800 tons of Cd (cadmium) have been deployed. “[ISWA and ipv 2017]. This becomes particularly problematic when it comes to the disposal of the modules at the end of their 25-30 years lifetime.
Despite the existence of legal disposal regulations, large quantities of old PV modules are not disposed of properly and still end up in landfill. The absence of economically viable recycling processes leads to a deficit of corresponding industrial processes in waste management. The separation of the individual recyclable materials through treatment systems is very difficult, because of the complex composite materials, which are firmly fused together. The dumping of PV modules can lead to heavy metals being leached out by rain and weather. Even though landfills have extensive protective measures, toxic substances can still be released into our atmosphere.
We are only at the beginning of the disposal challenge for solar modules, because the solar boom just started around the 2010s. According to statistics from the International Renewable Energy Agency (IRENA) from 2016, up to two million tons of PV waste are expected to accumulate by 2030, and 60 million tons by 2050. Without globally unified standards in waste management, the risk from toxic materials such as lead will become increasingly important.
RoHS directive without impact for solar technology manufacturers
There is already an international regulation called the RoHS directive (“Restriction of Hazardous Substances in Electrical and Electronic Equipment”), which prohibits environmentally harmful substances in products and thereby encourages the use of alternatives. However, the directive allows for exceptions, which also apply to solar modules. For instance, the use of lead and cadmium in PV modules is not bound by the RoHS Directive, and are still permitted without restriction. This decision should be seen critically, because the target for every manufacturer of photovoltaic solutions must be that the production, usage and disposal have a minimal environmental impact.
Organic solar technology
Organic PV can offer an environmentally friendly PV solution. The core of the solar film consists of organic materials, protected by PET foils. This enables simple and environmentally friendly disposal at the end-of-life of the PV module. The low use of materials and energy consumption for production, as well as the absence of rare earths and toxic heavy metals, such as lead and cadmium make this solar energy solution a truly green product.
TÜV-certified sustainability
At Heliatek, we have had TÜV Rheinland independently test the potential environmental impacts of our products via a Life Cycle Assessment (LCA). All phases of the product, from manufacture to disposal, were examined and evaluated. Every potential impact factor that might affect the environment was considered. This includes all energy and material flows, taking into account all transports during the life cycle. This comprehensive assessment also takes into account the issue of end-of-life disposal.
The TÜV Rheinland Life Cycle Assessment has certified the environmental impact of HeliaSol with under 16 kg CO2e/m². At very sunny locations, the product can achieve an extremely low carbon footprint of up to 3 g CO2e/kWh, and below 10 g CO2e/kWh at many sites worldwide (see figure 1).
The compact roll-to-roll manufacturing process, meanwhile, with its low-temperature process requires less than six months to generate the energy required for the entire product life cycle (Energy Payback Time).
Producer responsibility for this comprehensive view of potential environmental impacts should generally become more important in solar industry. In terms of climate protection, sustainable solutions should be promoted more intensively. After all, climate change can only be stopped by an energy transition – our future belongs to renewable energies such as solar energy.
About the authors
Stephan Kube is responsible for Marketing at Heliatek and has more than 5 years of experience in the solar energy industry. Susanne Müller is part of the product development team and conducted out the Life Cycle Assessment with TÜV Rheinland.
Also read
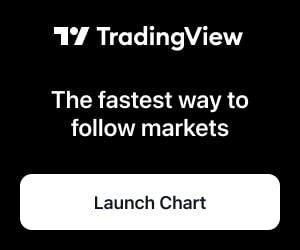