German Scientists Redesign Heap to Make Cheaper Redox Flow Batteries
- Scientists at the Fraunhofer Institute for Environmental, Safety And Security and Energy Technology UMSICHT, situated in Germany, declare that complete revamping the pile, they have contrived a way to bring down production costs of redox flow batteries which are made use of to keep renewable energy.
As a result, Christian Doetsch as well as Lukas Kopietz from Fraunhofer UMSICHT and also Dr. Thorsten Seipp from Volterion, that established the brand-new pile, have been granted with the Joseph von Fraunhofer Prize by the institute.
Prof. Doetsch discusses that the revamped stack is 40 percent more cost-effective in regards to material expenses. In addition, the pile weighs 80 percent less than a conventional stack and is only about half the dimension. It is being marketed by the spin-off Volterion. The Joseph von Fraunhofer Prize jury commented on the researchers' win by saying, "the spin-off as well as its effective exit from Fraunhofer, function as a prototype for marketing brand-new manufacturing technologies." The pile has been developed with an electrically conductive plastic to ensure that it remains flexible and can be bonded.
The German researchers laid out the procedure of making the gadget as follows: Plastic in the form of pellets is cooled to temperature levels as low as minus 80 degrees, after that ground into powder as well as blended with 80 percent graphite by weight. This powder is sent out with a system making up several rollers heated to various temperatures and also moving at different speeds. The powder is quickly melted between the rollers at moderate temperatures as well as low pressures. It is then massaged, rolled into an "limitless sheet" and also ultimately rolled up. Kopietz said, "This gives the new product polycarbonate properties, so it's flexible and also can be bonded although only 20 percent of it is plastic." The resulting flexible material is said to have thermoplastic residential properties as well as to be simple to weld, as a result of which the stack uses neither gaskets nor screws- the cells are simply bonded together.
One more reason production costs are decreased is because home plates can be created as a limitless roll through a powder-to-roll procedure, which requires a lot less product. The researchers explain, "Very slim plates can be generated this way. In the injection moulding procedure, home plate density is limited to numerous millimeters due to the production approach, but in the powder-to-roll procedure it can be between 0.1 as well as 0.4 millimeters." Subsequently, light-weight as well as discounted stacks can be produced.
Seipp said that this development opens absolutely new possibilities in layout, which have been implemented throughout to the full battery at Volterion. More than a thousand stacks have actually already been marketed by Volterion.
Also read
- Malaysia's Solar Ambition: 3 GW Storage Partnership
- Energy Vault And Astor Enerji Strike Cross-Supply Battery Partnership Deal
- United States Set To Add Thirty-Three Gigawatts Of Solar Capacity
- Reliance Infra Secures Major Solar-Storage Contract in India
- Iberdrola Pilots Agrivoltaics Above Basque Apple Orchards With Storage Project
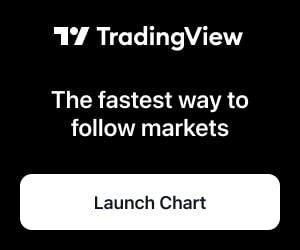