What You Need to Know about Field Inspection Software for Energy Companies
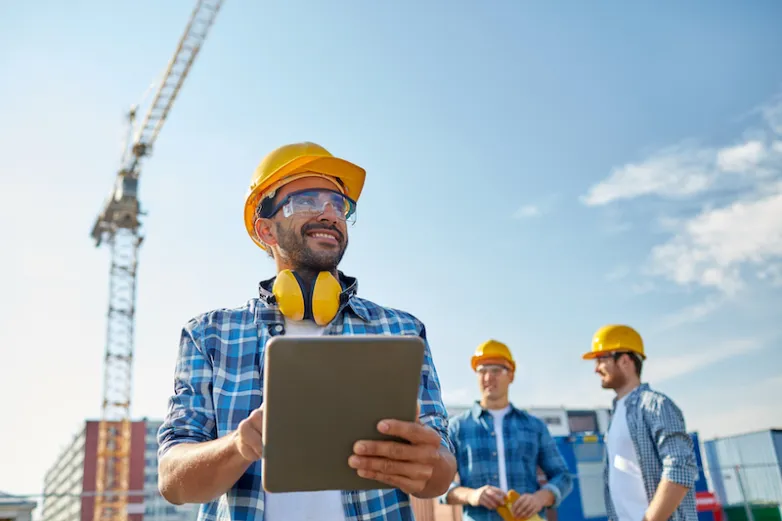
Project managers are responsible for ensuring project delivery in accordance with contract documents. This includes the plans or blueprints that detail how to build a facility, the specifications that indicate the materials to be used, and the contract that dictates payment and acceptance of the completed project.
You’re responsible for tracking project progress, including performance metrics related to the cost, schedule, and scope. Verification that the work is proceeding as per plan usually comes through inspection. This may include internal inspection from a superintendent or project engineer and oversight from an independent entity acting on your client’s behalf. It’s critical that inspections are conducted regularly, consistently, and formally. Here’s what you should know about field inspection software.
Why Is Inspection Necessary?
First, you must understand how crucial inspections are to success. No matter the size of your project, inspection is absolutely necessary. Imagine installing a system of pipes to drain a site for a windmill project. Without regular examination of the installation, you might not discover a faulty connection or improper installation until the area fails to drain after some rainfall. An inspection process usually identifies and documents the following:
- Confirmation that work is proceeding according to plan
- Compliance with building codes, owner specifications, and governing regulations
- Onsite conditions that are different from what’s indicated in contract documents
- Quality control problems in delivered materials and supplies
- Performance issues in materials testing and sampling, such as concrete and asphalt not meeting strength requirements
- Quality control problems in work by contractors and subcontractors
- Unsafe conditions or behavior in work zones
- Documentation of site incidents and occurrences that impact work execution
- Problems with equipment and tools
- Documentation of daily progress, including the number of workers, equipment used, items installed, weather conditions, and other details noted in a daily work report
- Advance notice of issues that may impact progress negatively or positively
Inspection is the main vehicle for monitoring and managing your energy project.
What About the Process?
A complex project may have multiple inspectors over its duration, which may be as long as several years. Two people can observe the same thing and capture different information without a consistent process. A uniform approach or inspection workflow means that no matter who’s doing the inspecting or where you are in the schedule, oversight is the same, making project audits and reporting easier. You may have multiple inspections depending on the type of oversight needed, but the value of a process is that it is documentable, accountable, repeatable, and verifiable. Consistent processes and workflows can take advantage of the power, flexibility, and convenience offered by field inspection software.
Your project requires different types of inspections. Some occur daily, while others take place at certain phases or milestones of a project. Some inspections may be required for activities of a certain level of complexity or risk. Let’s take a closer look at some of the most common inspection types.
Pre-Construction
This takes place before the contractor receives the official go-ahead to start the project. Pre-construction inspections are necessary because they allow you to accomplish the following:
- Verify field conditions are as indicated in contract documents
- Choose a location for a field office or project trailer, if necessary
- Check for appropriate staging locations for heavy machinery and large items, such as cranes or concrete girders
- Confirm overhead or underground utilities to be removed, adjusted, relocated, or abandoned
- Document pre-construction conditions to which the site must be returned before the owner accepts the completed facility
- Verify adjacent property owners and confirm stakeholders
Daily Work Report
These inspections capture information related to the work done each day, including laborer and subcontractor man hours, equipment used and status, materials delivered and installed, daily high and low temperatures, weather events, and other occurrences. Between the construction company staff and entities providing oversight, various people may be responsible for this type of inspection, making the need for field inspection software critical.
Safety Management
Safety is a crucial performance metric for any construction project. Safety inspections should be regularly conducted as part of an overall safety management plan. Your company may employ a safety manager or auditor who makes regular or random site visits to observe and record the following:
- Hazardous work conditions such as confined spaces, ladders, and scaffolding
- Unsafe behaviors by work crews
- Unsafe conditions, especially those created by third parties, such as drivers or property owners
- Confirmation of best practices, including OSHA training and wearing of personal protective equipment such as hard hats, steel toe boots, and protective eyewear
- Verification that field facilities are compliant with safety regulations, including unblocked exits, fire extinguishment systems, proper lighting, etc.
- Documentations of all the important details of a safety incident or violation
- Verification that corrective action has taken place
It’s in everyone’s best interest to prioritize safety. A safety inspection app benefits both those working onsite as well as anyone responsible for oversight and validation.
Quality Management
In addition to daily site inspections, an internal or independent quality manager may complete an inspection at pre-determined phases of the project, such as 30%, 60%, and 90% completion, or monthly, or quarterly, in accordance with the contract. A quality inspector may focus on certain aspects of the work, checking the completed elements against an owner’s specifications, building codes, or other local regulations.
Survey
An independent surveyor may be contracted to verify that the facility is built in the right place. This inspection would verify that the contractor has used the proper benchmarks and reference points. For horizontal construction, such as roads, bridges, and pipelines, a surveyor checks station locations, offsets, profiles, and elevations.
Materials Testing and Sampling
Inspection of materials through testing and sampling is a critical part of most construction projects. These inspectors test samples of wet concrete for plasticity, temperature, and moisture in anticipation of expected strength performance. Cylinders of concrete are tested for compressive strength at various points to confirm the expected design strength. You need inspection software to document samples and tests, especially if future materials performance is below or out of specification.
Critical Work Inspection
Work that is critical or unusual, or requires specialized methods, tends to warrant special oversight, for example, a bridge with an extra-long span that requires post-tensioned concrete piers, larger columns, special footings, and deeper foundations. Inspection software that integrates project schedules may ping a PM or superintendent to confirm the availability of additional inspectors for this specialized work.
Environmental Checks
Some construction jobs are subject to environmental restrictions, requiring close observation and checks for stormwater pollution, erosion control, concrete washout, trash disposal, and more. Environmental inspection software may be a sub-module of a safety inspection app that also sends alerts should an inspector note a violation or deficiency.
Project Closeout
Before a client can take ownership of a completed facility, a substantial or final walkthrough is usually required. The contractor and oversight personnel will go over the project and create a punch list of items to be completed. Your team could use software to outline the work to be completed specifically for a final inspection as well as other project management items to be resolved during the closeout phase.
What Are the Essential Features of Field Inspection Software?
Personnel can certainly benefit from a powerful, well-designed software solution, especially for conducting site inspections, generating reports, and distributing them to interested parties and stakeholders. An effective platform should offer these advantages:
- Full functionality on mobile devices such as laptops, smartphones, and tablets, irrespective of operating system
- Interoperability and uniformity across operating systems and devices
- Fully integrates with device features such as taking photos, capturing video, and recording sound
- Cloud-based architecture, eliminating the need for hard copies that take up space and are vulnerable to destruction and loss
- Various levels of access and control tailored to your operational needs
- Ability to create templates that are customized for the project and the type of instruction
- Quick generation of electronic forms to be completed by an inspector in real time out in the field
- Distribution of completed forms to appropriate personnel for review and approval
- Automation of inspection processes and workflows
- Notification of appropriate personnel when reports are not approved or signed, or violations or deficiencies are recorded
- Integration with other project management functions and metrics, such as schedule updates, resource allocation, cost control, change order management, auditing, etc.
- Generation of reports based on types of inspection
Inspection software must be lightweight, flexible, and scalable, easily modified based on project complexity, resource availability, and other project features. Your software solution needs to be intuitive, easy to deploy within your organization, and easy to use.
Inspection reports are the backbone of your project’s progress. Regular, consistent completion helps you stay on top of your project’s needs, anticipating issues and solutions in advance. An inspection software platform maintains a record of every inspection that can be accessed, audited, and distributed in accordance with owner preferences, contractual requirements, and corporate objectives. The best software approach facilitates real-time usage so your inspectors don’t have to recall details from their memory or handwritten notes.
Also read
- The Academic Importance of Case Studies in Energy Efficiency
- Integrating IoT Technology in Solar Energy Monitoring Systems
- How To Avoid Plagiarism In Academic Writing: Essential Tips To Avoid Problems
- Best AI Detection Tool for Students: Explore EssayPro’s Solution
- Why I Chose to Pay Someone to Write My Paper (No Shame)
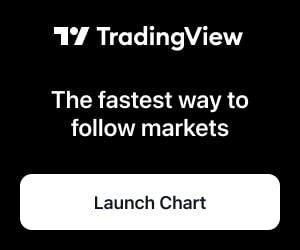