EV Battery Makers Are Obtaining Their Hands on Everything
- Shortages are striking the entire electric vehicle supply chain-- and also currently even easy-to-source aspects like graphite are proving pricey.
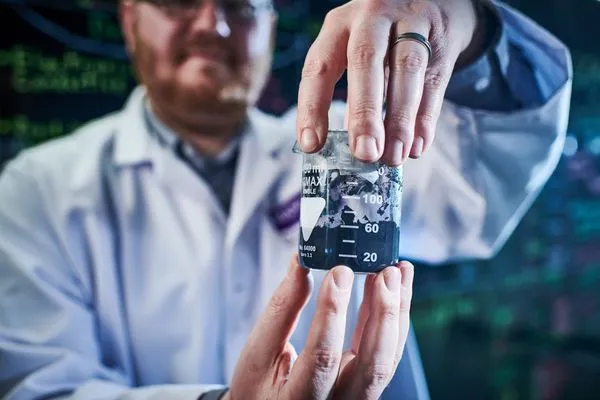
By Anjani Trivedi
Among the most plentiful and also crucial ingredients in electric vehicle batteries is starting to experience need stress, showing how supply chain troubles are obtaining much deeper and the value chain much more costly.
Tesla Inc. last week signed a take care of Australian mining firm Syrah Resources Ltd. to obtain materials from the firm's Louisiana operations, with the raw inputs originating from Mozambique. Meanwhile, South Korean company POSCO, the largest all-natural graphite anode manufacturer internationally, got a 15% stake in China's Inner Mongolia Sinuo New Material Technology Co. Hong Kong-listed Graphex Group Ltd. lately established an U.S. subsidiary and also is aiming to develop a plant there. It also inked an agreement with German firm Desatec GmbH for handling and marketing graphite materials as well as developed a neighborhood production arm. Various other, smaller companies are only now building facilities in North America.
This flurry of very early-- and prescient-- moves by some makers to obtain their hands on materials as standard as graphite make it clear: This is no more almost higher-value and harder-to-get steels like lithium and also cobalt. Supply shortages are coming for the entire EV battery supply chain, just as firms like Tesla are offering document varieties of environment-friendly vehicles. From lithium substances and also spodumene to PVDF 1-- all raw components for batteries-- costs over the last year have actually climbed by as much as threefold. Currently, graphite is beginning to see the surge also.
A kind of carbon, graphite is indispensable for making the anode, or the negative incurable, in powerpacks and also is additionally utilized in steelmaking as well as the nuclear market. Virtually 90% of production is focused in China, meaning yet an additional key part of the battery is made in the country that's already experiencing disturbances because of break outs of omicron in crucial commercial areas like Tianjin. The majority of new graphite electrode ability is additionally generated in the world's second biggest economic climate, according to BloombergNEF information, adhered to by Japan, India and the U.S.
Until now, much of the emphasis in next-generation batteries has actually gotten on the cathode material side of points-- nickel cobalt manganese, lithium iron phosphate and more. Couple of have actually focused the anode chemistry mix, with graphite expected to continue to be the leading material until a minimum of 2035, according to BloombergNEF.
With demand for batteries remaining to increase on the back of electric vehicle exhilaration, ability in this part of the supply chain will need to raise also. Most of it will be for automobile.
The material happens normally but is additionally produced artificially. It isn't easily exchangeable, though, which places additional pressure on costs. Over the past year, costs for synthetically constructed graphite have enhanced between 6% (for the high-end range) to around 40% (mid-range). That's also as producers in China have been able to bring down the price of graphitization-- a crucial procedure that represents around half the cost of an anode-- by as much as 15% to 20%. A quarter of the price is raw materials. If makers aren't able to keep prices down while they try to broaden capability, battery expenses will just maintain increasing. That will make it tougher to develop out supply chains-- also globally.
At this point, stakeholders in the electric vehicle market that have actually been slow-moving to catch up, consisting of automakers and also battery makers, can't simply begin to claim future supply-- they might obtain left. They'll have to believe years ahead and also begin spending means down the value chain, not simply in expensive tech gadgets as well as batteries in its entirety.
In the past, investing in, and also planning for, core materials like graphite seemed unneeded-- the availability was taken for granted. Now, with the shortages and also supply chain snarls here to remain, it simply feels like a reasonable and sensible service technique.
Also read
- Finland Greenlights Korkia's 80-MW Solar-Battery Project
- Pacific Green Secures $50 Million Loan For Australian Storage Projects
- UK planning approvals for renewables smash records as storage surges
- U.S. solar build stays on record pace despite policy crosswinds
- Malaysia's Solar Ambition: 3 GW Storage Partnership
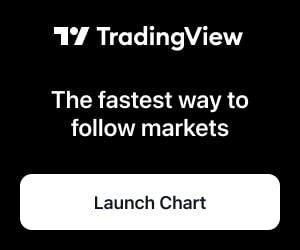