Energy Saving Tips For Manufacturing Facilities
When it comes to manufacturing, one of the most significant expenses for businesses involved in manufacturing is industrial energy costs, regardless of the shape and size of the business. As a manufacturer, you need huge amounts of energy to run the production process. You need energy for lighting, cooling, heating and other processes. However, saving money on energy can go a long way in improving your bottom line leading to higher profitability. If you haven't formulated a plan to bring down your energy costs, now is the time to get started.
One of the ways to identify opportunities for saving money on energy is through an energy audit. In the audit, the production line equipment, HVAC and lighting systems are closely inspected and evaluated. Some manufacturers prefer using an internal team for conducting an energy audit but in case you do not have experienced members for managing the process, consider taking the help of energy experts. Whether you choose to have an internal team or energy experts, here are a few tips on reducing your energy costs:
#1 Check for Leaks in Compressed Air Systems
It's obvious that leaks can lead to significant waste of energy and fixing those leaks can help you save quite a bit of money. Research suggests that a compressor's output is affected anywhere from 20 to 30% when there is leakage. It not only leads to higher energy costs but also affects the efficiency of the equipment.
There are many ways to check leakages in the system such as an air leak survey. Smaller leaks can be detected with the help of ultrasonic detection equipment. Some of the most common causes for air leaks include worn out materials, loose hoses and tubes as well as missing seals or welds. Fixing these leaks will depend on the cause but in many cases it can be as simple as just replacing minor parts or tightening of fittings.
#2 Equipment Upgrade
You need to ensure that the equipment is always in excellent working condition in order to achieve maximum energy efficiency. Retro commissioning involves looking at the equipment in your manufacturing facility in a systematic manner to find those that are performing below optimal levels. Any inefficient or outdated equipment must be replaced.
There could be many causes of energy wastage other than the manufacturing equipment used in your facility. Investing in a new HVAC system might not be practical for everyone but savings from upgrading existing equipment such as computers, monitors and ceiling fans can save a lot of money in the long run. You must come up with a schedule for proper evaluation and maintenance of all the equipment and not just the main equipment.
#3 Energy-Efficient Lighting
High quality lighting is critical to manufacturing facilities and therefore, it's important to properly install energy-efficient lighting. Light emitting diodes or LEDs as well as compact fluorescent light bulbs or CFLs can help save quite a bit of money on lighting costs.
Another way to save money on lighting is by removing or turning off lights installed in non-essential areas. For instance, vending machines are common in manufacturing facilities. These vending machines should be placed in well-lit areas and their individual light bulbs can be removed to save money on lighting.
#4 Powering down Equipment
You will notice that every single piece of technology used in a manufacturing facility uses electricity for energy. It might seem obvious to shut down this equipment when the day is over but it is often overlooked. When employees are not working, whether they are on an extended vacation or it’s over night, they should remember to shut down the computers as well as other equipment or at least, ensure the equipment is placed into sleep mode. If your manufacturing facility uses networked computers, the IT administrator can make them more efficient by adjusting power settings.
These small savings add up over a period of time. For instance, if the cost of electricity in your location is $0.12 per kilowatt hour, you can save at least $3400 a year by reducing consumption by 2400 kWh a month. These savings can be used for upgrading the equipment thus starting a virtuous cycle leading to lower energy costs.
#5 Improvement in Process Heating
Typically a third of the energy usage of a manufacturing facility can be attributed to process heating which is essential for making most of the industrial and commercial goods. Significant energy savings can be made in this area by:
- Installation of waste heat recovery systems
- Using alternative fuels that have higher combustion efficiency
- Installation of automatic blowout control systems
- Control of exhaust gases
- Ensuring proper furnace installation
#6 Paying Attention to Energy Consumption Periods
An energy audit should be conducted to figure out the time during which most energy is used along with the processes responsible for maximum energy usage. It will help in evaluating whether you can change things to save money on electricity consumption.
Electricity rates vary and typically, depend on the time during which energy is consumed. The peak electricity rates typically happen in the afternoon and early evening hours. You can save some money by avoiding the peak period rates by adjusting your operating hours.
#7 Convincing Your Employees
You want to bring down the energy costs but it's not going to happen unless you convince your employees. You need to communicate in the right manner about the need for reducing energy consumption. You need to convince employees by communicating clearly how these savings are going to benefit their work life. For instance, you can tell them that savings made by reducing energy consumption will be used for new equipment that will make their job easier. When you get the employees involved, it will also empower them to come up with new ideas.
The energy consumption and corresponding expenses of your business can be brought down by designing and executing a comprehensive energy strategy for your business.
Also read
- EPA Halts $7 Billion Solar Program Amid Legal Hurdles
- SMA Solar Suffers Loss Amid Weak Home And Business Demand
- ENEOS Partners with West Energy on Tohoku Micro-Solar Expansion Drive
- SolarEdge rapidly ramps Utah plant, starts shipping USA-made home batteries
- E.ON UK’s £4 m Bet Unlocks Solar for Flat-Dwellers
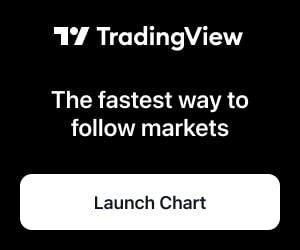