DuPont on the hunt for Aussie field survey partners
Oct 16, 2019 02:59 PM ET
- Over the last decade, DuPont has surveyed more than 2 GW of PV installations and has analyzed a range of failure types and their causes. Hong-Jie Hu, DuPont’s solar technical and development lead in China, says that the materials giant is looking for Australian partners for its Global Field Survey program, with a particular interest in hot and humid and desert environments.
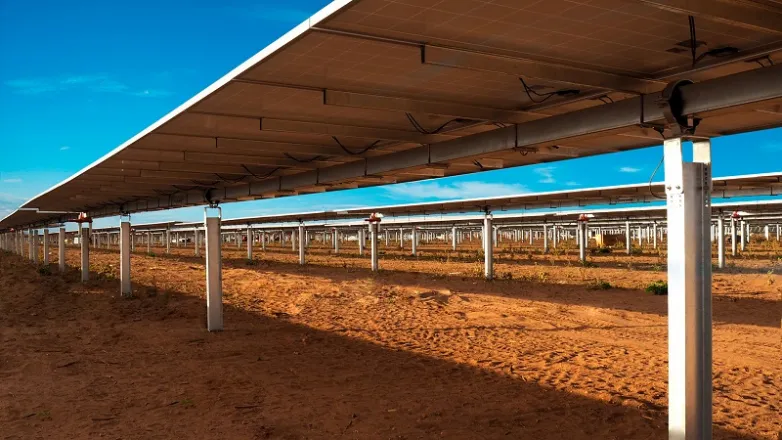
pv magazine: DuPont’s field survey has become one of the largest of its kind, in terms of understanding PV system failures. Is it currently collecting data from the Australian marketplace for its Global Field Survey? And what is it revealing?
Hong-Jie Hu: In our database, we do have a few cases from Australia – but not so many. There was one case in Australia that was a large-scale solar farm with backsheet inner-layer cracking issues – causing losses for the owner. We do have interest in having more field cases in Australia and we are also looking for partners in Australia to cover the field study in Australia.
We are looking for partners who are familiar with the Australian market, have connections to the solar farms. It has become one of my missions.
Bifacial module uptake has been strong in the Australian marketplace, with some of the largest bifacial projects outside of China currently being developed. DuPont has been promoting Tedlar-based transparent backsheets as a good option for module suppliers to meet this demand. Why is it that you believe that transparent backsheets are better than glass-glass?
We believe there are a lot of advantages, compared to glass-glass bifacial modules.
We have compared weight, durability, and also O&M [operations and maintenance] advantages and disadvantages. A bifacial module with transparent Tedlar-based backsheet is lighter in weight, easier to install and maintain, and more durable in the field..
These three benefits bring a lot of value to the downstream customers and to module makers as well.We also bring some potential cost reduction possibilities for the module maker in manufacturing as transparent backsheet could be used withexisting manufacturing lines – there is no need for modifications – as is the case with glass-glass modules. For weight, a 60-cell bifacial module 2.5mm glass-glass is about 24-25kg and Tedlar-based backsheet module is only 18-19kg. So, the weight difference is more than 30%. For 72 cell is a similar trend, [weight for glass-glass is] always above 30%, which is a big difference, resulting in lower transportation cost and installation cost.
What are some of the manufacturing cost advantages of transparent backsheets?
This depends on individual module maker customers, because their lines all have different processes, different quality control criteria. But speaking roughly for the module production side, transparent backsheet it can ensure higher productivity and yield rate. Glass is brittle and must be handled carefully during transportation and lamination. Also, the lamination speed is lower for glass-glass module production, resulting in lower capacity, which is a big loss for module makers as supply is tight now for bifacial modules. For transparent backsheet is just the same as white backsheet.
In terms of weight, there are some very thin glass coming onto the market. Doesn’t this cancel out the weight advantage of transparent backsheets?
We have heard some voices from the market, some module makers, that they consider [to use] 2mm thin glass. But even with 2mm glass, modules are still more than 10%-15% heavier than [a module using] transparent backsheet. For the thinner glass there are also huge concerns about the mechanical properties.
Most of the thinner glass, like 2mm or 2.5mm glass on the market, is not a real tempered glass – it is a semi tempered or heat strengthened. So, the hardening and the mechanical properties are much lower. Also, there is only very small capacity of 2mm tempered glass on the market and that makes it much more expensive. The tempering process is quite different for 2mm glass than 3.2mm glass. The thinner glass needs a gas floating tempering system, this requires new processes, new investment and production capacity.
Is there a trade off between transparency and durability? We all understand glass and light transmittance pretty intuitively. How does that relationship play out?
Light transmittance is an important consideration. Firstly, the durability is not a consideration that can be compromised for a backsheet. We use very high grade UV stabilizers and we make sure the durability is of a very high standard. And for light transmittance we can achieve more than 92% for Tedlar film. When laminated with the backsheet, the transmittance can achieve 91-92.5% for the backhseet.
For glass, people usually don’t use ARC [anti reflective coating] on the rearside. So, the glass can only achieve around 91% in light transmittance. The transparency of backsheet is comparable but in some places it is slightly higher than rear glass.
Glass more generally is often promoted as being particularly robust. How do transparent back sheets perform in terms of reliability with conventional back sheets?
Durability is the most important thing we consider in the R&D period. For the white Tedlar [material] it has more than 30 years of track record in the field and has a good reputation. So, we did a lot of work on the durability, not to damage that brand. We have very strict internal testing standard for all of the film and backsheet. For that testing we use four types of UV resources, respectively and test up to 4000 hours UV ageing.
We also conduct around 3000 hours damp-heat ageing test. Then we send the sample into mini module for sequential ageing test. That is DuPont internal test standard. And only then we can have confidence about the reliability.
In summary, we believe the durability of transparent backsheet is as good as, if not even better than white Tedlar backsheet, which has been proven in the field can last more than 30 years. While we have found many field failure cases of old G/G module while module with new thinner glass and POE is new to the market and the design keeps changing as new issues keep popping up.
How do very hot or very hot and humid environments impact on Tedlar based transparent back sheets?
Tedlar PVF film is very stable in all kinds of climates. For transparent backsheet we conducted so much endurance testing so that we have confidence. Damp heat 3000 hours represents >25yrs damp heat stresses in any places in the world, we don’t even recommend that for module testing.
We also considered desert climates in our development – very hot and dry, and with sand abrasion. We conducted sand abrasion test and the light transmittance after sand abrasion – with the decrease of under 1% even after 100 liters of sand ablation.
Given this lengthy testing process, how long did it take to bring the Tedlar, transparent backsheet to market?
Firstly, we are not a startup going from zero on this. We had a previous version of the transparent film from 20 years ago. We had field proven records in Europe which had used transparent Tedlar backsheet – and they still work well in many places. About three years ago we started the work on the new generation of transparent films. Then working with the laminators took another a year.
There appears to be a number of transparent backsheet products coming onto the market. How do they vary?
We keep a very close monitoring of that. Our conclusion is that they are not really ready, so far. For example, we tested several different kinds of transparent backsheet, PET based, PVDF and coating based. PET based has shown some yellowing issue or a light transmission decrease issue after aging tests. For the PVDF film based backsheet, we have seen that it is very brittle – more than even the white ones. There is a high risk of cracking in the field. For a coating based backsheet has some UV resistance issue and sand abrasion resistance is very poor.
You’ve mentioned earlier O&M advantages for use of transparent backsheets. What are they?
We talk about the transparent backsheet being lighter, more reliable and easy cleaning. In terms of O&M the Tedlar is a fluorine material and it has high surface energy. For high surface energy material the water contact angle is small and presents as hydrophilic. It is proved through testing and is a characteristic of easy cleaning. Tedlar film has other applications, like we use it as an interior material for aircraft and building, because it is easy to clean and is durable. Tedlar surface is easier cleaned than glass or even self cleaning. That means that the dust or soiling can be easily removed by blowing wind or rain/water. That can bring benefit for [PV project] owners due to more power generation in the field from the rear side.
Another case is that the transparent Tedlar backsheet brings benefits for tracker systems. I have seen a lot of failures in the field for glass-glass modules on trackers. Transparent backsheet module is lighter which may reduce tracker load and failure rate and requires less power consumption.
Hong-Jie Hu will speak at the pv magazine Quality Roundtable event at All Energy Australia on Oct. 23. Register here to attend. He is the Greater China Technical Service & Development Leader, Tedlar & Fortasun, for DuPont Photovoltaic and Fluoro Materials.
Also read
- Exploring the Key Players in Dubai’s Solar Panel Distribution Market
- Solar Site Selection: How to View Historical Satellite Images To Track Land Changes Over Time
- SEF 2025 Kyiv: Forum on Innovation and the Restoration of Ukraine’s Energy Sector
- Innovation and Sustainability Arrive in Bucharest at the Country’s Largest Exhibition for Green Technologies and Solutions
- Energy risk management: How businesses can protect themselves from market volatility
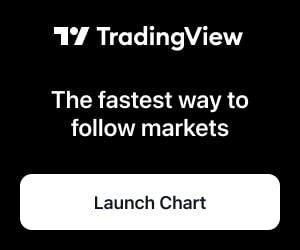